“BIM is the first truly global digital construction technology and will soon be deployed in every country.” This statement highlights the game-changing role of Building Information Modelling (BIM) in the construction industry.
BIM is reshaping how construction teams collaborate, plan, and execute projects. The tool creates detailed 3D models, streamlines workflows, and empowers teams to make smart and fast decisions while minimising errors and reducing costs.
As the industry evolves, BIM enhances projects’ completion and sets new standards for efficiency and quality in construction. In this article, you’ll learn how BIM helps construction practices, from the earliest design stages to the final touches of facility management. Let’s start.
Strengthening Collaboration and Communication
Building Information Modelling (BIM) improves teamwork and communication during construction. Everyone works on the project in a shared digital space to collaborate efficiently and stay aligned. This improved teamwork helps the project run more smoothly, efficiently, and successfully.
In a BIM system, everyone can view and update the digital model in real-time. They always have the latest information, whether in the office, on-site, or working remotely. It helps avoid misunderstandings, miscommunication, and delays caused by outdated designs or conflicting details. We can record design changes and versions with the help of BIM with the name of the owner responsible for updates.
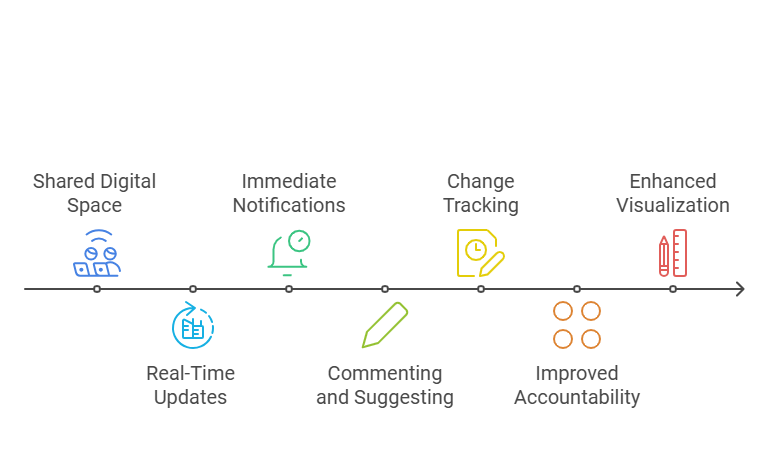
For instance, if an Architect changes the building’s facade, the update shows up immediately in the shared model. A structural engineer can then check if the change affects the building’s safety, and a contractor can adjust the construction schedule.
In addition, BIM improves project coordination by letting teams mark/tag/leave comments, notes, and suggestions directly in the model. It reduces the back-and-forth typically found in older processes, where information might get delayed or lost while passing through multiple channels.
Another advantage is BIM’s ability to track and document changes. Every update to the model is recorded, showing who made the change, when, and why. This transparency improves accountability and makes sure no important details get missed. It helps the whole project team stay on the same page.
In addition, BIM helps construction by improving visualisation, removing clashes, refining BOQ & BOM and design, and paving the way for more efficient, cost-effective, and innovative construction processes. Let’s understand how!
Enhancing Visualisation and Design
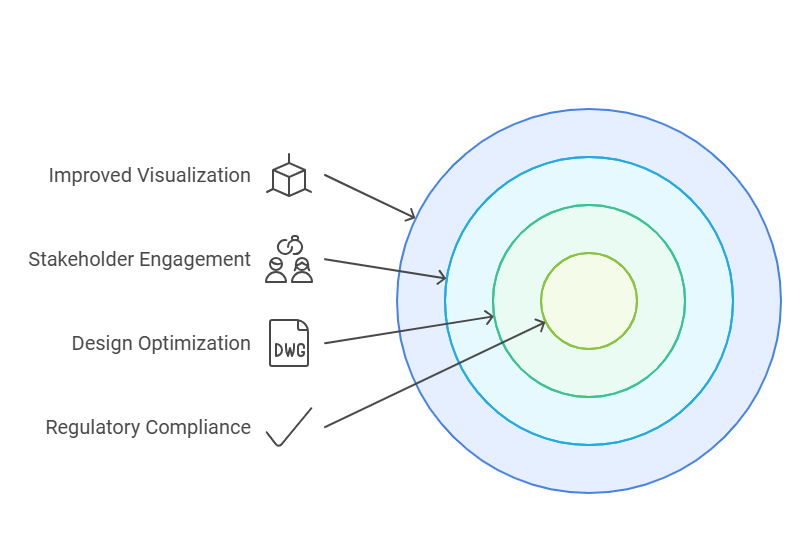
Building Information Modelling (BIM) uses advanced digital tools to create detailed & realistic 3D models of buildings or infrastructure. These models let Architects, Engineers, Contractors, and Clients explore the project digitally by rotating it, zooming in, and viewing it from different angles.
BIM’s 3D models go beyond visuals and include material quantities, joineries, details, structural components, and mechanical systems. This level of visualisation is beneficial for stakeholders like clients, investors, or regulators who might not have technical expertise.
BIM helps them understand the design, project scope, design flaws, and potential challenges more efficiently, which leads to good decision-making. You can easily spot design flaws, aesthetic issues, or other problems early.
For instance, a client can virtually walk through the building to see model and equipment placements or feature alignments & request changes in real time.
With BIM, designers and engineers can visualise how rooms, floors, and systems work together in real space. They can consider both physical dimensions and functional needs, such as flow, accessibility, and utility. It helps optimize layouts, improve functionality, and create a better experience for building users.
BIM models can also account for real-world factors like building codes, site conditions, and structural limitations. It ensures the design meets aesthetic, functional, and regulatory requirements. By identifying and solving potential issues early, BIM reduces the need for expensive revisions later in the project.
Streamlining Clash Detection
BIM improves design quality through clash detection, identifying conflicts between building systems before construction begins. Detecting these clashes early means teams can fix them before construction starts, saving time and money by avoiding later rework and delays.
Clash detection uses the 3D model to check for spatial conflicts between building elements. For instance, an electrical conduit is positioned where a ventilation duct is planned, or a structural beam interferes with a plumbing pipe. Then, BIM flags these conflicts automatically and this defect can be rectified before actual construction begins.
Teams can then adjust the design before construction starts. By resolving the issues, clashes, record design updates early, BIM minimises the need for expensive changes and redesigns later. Clash detection also enhances safety by reducing the risk of structural or operational problems on-site.
Now, let’s move ahead and discuss how BIM allows efficient resource management.
Optimizing Resource and Risk Management
BIM helps construction by managing resources and risks throughout a project’s lifecycle. It provides real-time, data-driven insights and helps with accurate planning, better cost management, and proactive risk mitigation.
BIM integrates quantity take-offs, material scheduling, cost estimation, and risk identification. It ensures resources are used efficiently, budgets are met, and potential risks are addressed early.
Precision in Quantity Take-Offs and Material Scheduling
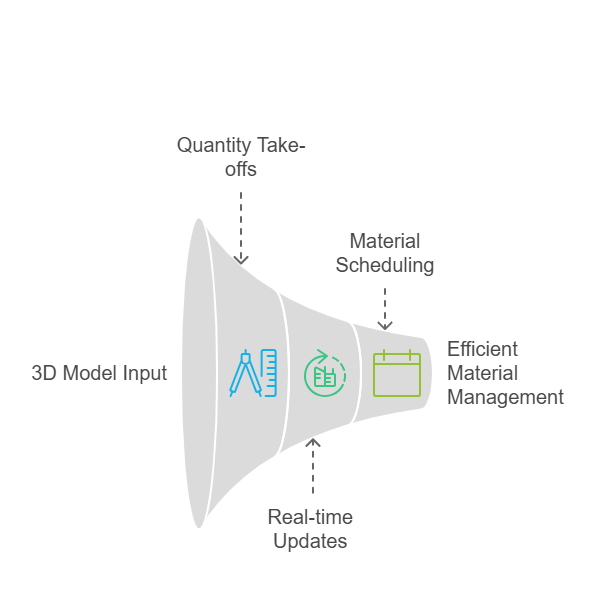
BIM automates and streamlines quantity take-offs and material scheduling. The quantity take-offs get automatically generated from the 3D model.
It provides precise and detailed material lists that include exact quantities of concrete, steel, timber, plumbing fixtures, and more. As the design changes, the BIM model updates these quantities in real-time to ensure that estimates are always up to date.
BIM also facilitates material scheduling. It helps project teams plan when and how to deliver materials to the site. By factoring in lead times, storage needs, and construction sequencing, BIM ensures that materials arrive timely, in the right quantities, and in the proper order. It minimises the risk of shortages or excess materials, which can cause delays and waste.
Accurate Cost Estimation with 5D BIM
BIM’s ability to integrate cost data into the 3D model improves cost estimation and budgeting by adding a fifth dimension, 5D BIM. With 5D BIM, cost estimation gets directly linked to the 3D model.
As the project progresses, BIM automatically updates the cost estimates based on the quantities of materials, labour, and other resources needed for each design element. This integration enables real-time tracking of costs and ensures that design changes, such as adjustments to materials or systems, are instantly reflected in the budget.
For instance, if a design change calls for additional steel or concrete, BIM will quickly recalculate the cost impact and adjust the budget accordingly. It helps project managers immediately assess the effect of design changes on the overall budget.
5D BIM also improves budgeting accuracy by considering labour productivity, overhead, and time-related expenses. With this more precise data, stakeholders can avoid cost overruns and keep the project on budget.
Reducing Project Risks Effectively
BIM plays a crucial role in efficient resource management and risk mitigation by reducing the chances of rework and design errors in construction projects.
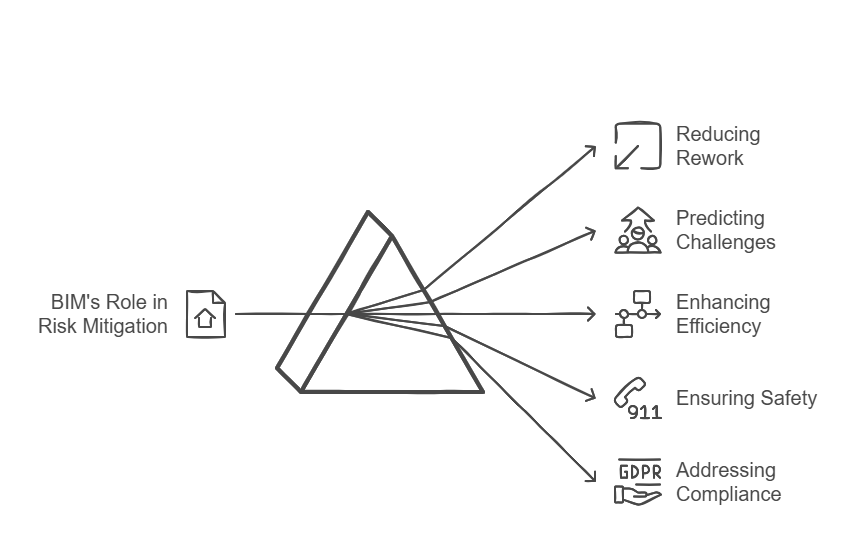
BIM helps construction by enabling virtual construction simulations that predict challenges and inefficiencies before they arise on-site. It addresses potential delays and conflicts early, reducing the risk of disruptions during actual construction.
BIM also ensures the design is functional and cost-effective by optimising constructability. It allows for prefabrication of building components off-site, which reduces on-site rework and enhances project efficiency.
Beyond reducing rework, BIM helps mitigate other project risks, such as safety hazards, delays, and compliance issues. It simulates site conditions, identifies potential hazards, and plans for safer construction practices.
Let’s move ahead and discuss how BIM supports sustainability.
Advancing Sustainability and Performance Evaluation
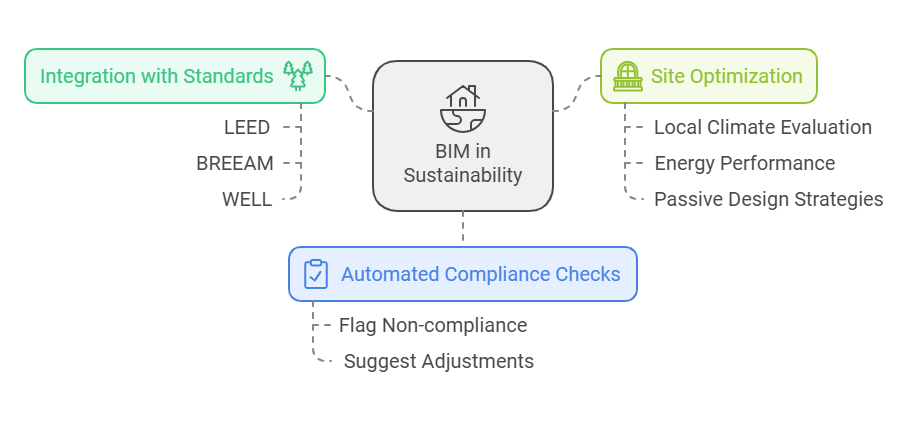
BIM offers essential tools to evaluate, optimise, and monitor sustainability efforts throughout a project’s lifecycle. It enables teams to make data-driven decisions that lead to more efficient, eco-friendly, and durable buildings.
BIM integrates with environmental performance standards and certifications such as LEED (Leadership in Energy and Environmental Design), BREEAM (Building Research Establishment Environmental Assessment Method), and WELL.
These standards are embedded within BIM tools that enable automated checks against sustainability goals and compliance with environmental regulations. As the design evolves, the system can flag non-compliant elements and suggest adjustments to meet sustainability targets.
Additionally, BIM supports optimising building siting by evaluating the site’s unique environmental context. For instance, the model can assess how local climate conditions like temperature, wind patterns, and solar exposure affect the building’s energy performance. It guides decisions on the building’s orientation, insulation, and passive design strategies, improving its sustainability.
Maximizing Energy Efficiency
One of the most significant advantages of BIM in promoting sustainability is its ability to optimise energy efficiency through detailed simulations. BIM integrates energy analysis directly within the model and provides continuous, real-time feedback on a building’s energy consumption and performance.
BIM-based energy simulations assess how a building’s design influences energy demand and operational efficiency. Factors like thermal performance, daylighting, ventilation, and insulation determine areas where you can reduce energy usage.
Building Energy Modelling (BEM) tools within BIM can simulate a building’s energy consumption under various operational scenarios. It allows teams to optimize heating, cooling, and ventilation systems. BIM software can also simulate integrating renewable energy sources to ensure optimal performance in specific climates and configurations.
For example, solar radiation analysis can inform decisions about the placement of photovoltaic (PV) panels. It minimises the building’s energy use while maximising energy generation. This approach can significantly minimise reliance on fossil fuels, lowering operating costs and the building’s carbon footprint.
BIM can simulate HVAC (Heating, Ventilation, and Air Conditioning) system efficiency, evaluate the impact of system layout and integration, optimize airflow, and reduce energy consumption.
By embedding energy analysis into the design and construction phases, BIM enables teams to implement energy-saving strategies earlier in the project. It reduces the need for costly retrofits and improves operational efficiency once the building is in use. BIM Supports GREEN EARTH INITIATIVE.
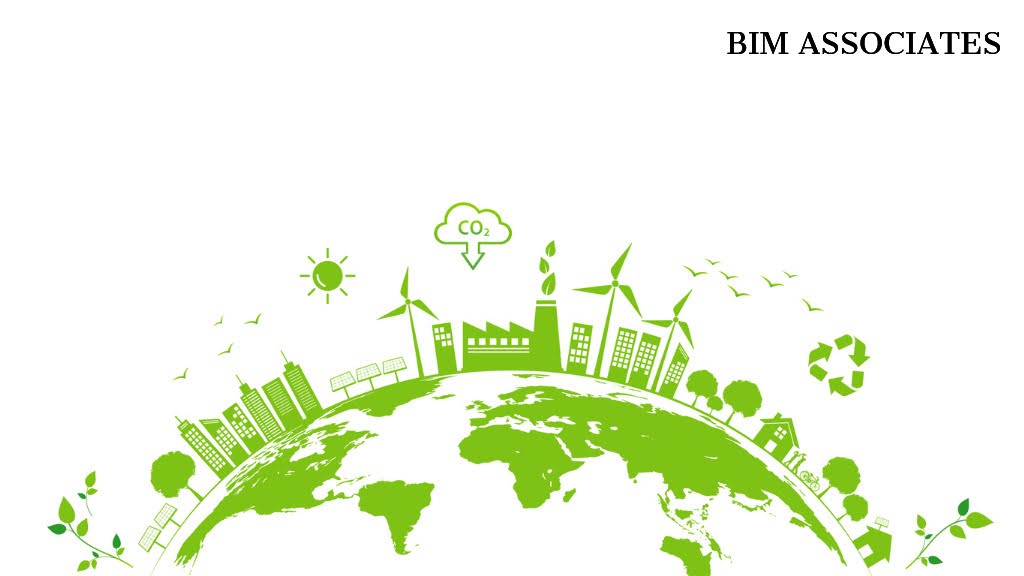
Lifecycle Analysis for Sustainable Solutions
BIM supports lifecycle assessments, which look at the environmental and economic effects of a building throughout its life. It helps project teams evaluate the long-term sustainability of their designs by simulating how materials, systems, and the building will perform over time.
Lifecycle assessments within BIM tools take into account a range of factors, including:
- Durability – How long materials and systems will last and how often they need to be replaced or maintained.
- Operational Energy Use – The building’s energy consumption over time, including how well passive design, renewable energy systems, and energy-efficient technologies perform.
- Waste Generation – The waste created during construction, operation, and demolition, as well as ways to reduce and recycle waste.
- End-of-Life Considerations – Disposing or repurposing materials when the building’s useful life ends.
Let us now discuss how BIM helps streamline project timelines and enhance efficiency.
Streamlined Construction Sequencing and Off-Site Methods
BIM helps construction by offering a detailed and dynamic framework for planning projects. It improves site logistics, scheduling, and the use of prefabrication. By combining digital modelling with precise scheduling, BIM makes construction more efficient, cost-effective and coordinated.
Detailed Construction Sequencing with 4D BIM
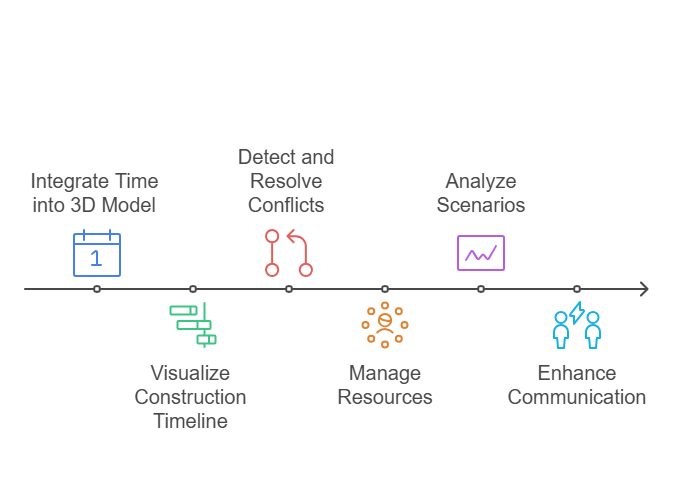
One of the key innovations in BIM is the addition of 4D BIM, which incorporates time into the traditional 3D model. This powerful tool allows project teams to visualise and simulate the construction process.
It also shows how each building component gets constructed over time. By connecting the 3D model to the project schedule, 4D BIM provides a dynamic, real-time view of construction sequencing, improving planning and coordination. Here are the primary benefits of 4D BIM for construction sequencing:
- Visualisation of Construction Timeline – 4D BIM allows stakeholders to see the project’s progress over time, with each construction activity in the 3D model at the right stage. It helps the team understand the task sequence and ensure everything is done in the correct order.
- Conflict Detection and Resolution – By linking the schedule with the 3D model, 4D BIM helps identify potential conflicts between tasks, spaces, or construction phases. For example, two activities, like crane operations and material delivery, are scheduled at the same location at the same time. In that case, the clash can be spotted and resolved early, preventing delays and rework.
- Improved Resource Management – 4D BIM helps project managers optimise labour, equipment, and materials resources. The model shows when you’ll require resources at different stages. It helps to avoid underuse or overuse, leading to more efficient labour and equipment scheduling.
- Scenario Analysis and Planning – 4D BIM allows project teams to run different scenarios, exploring how different sequencing options affect the overall schedule. It helps optimize construction phases, minimise downtime, and adjust timelines to ensure timely completion.
- Enhanced Stakeholder Communication – 4D BIM improves communication with clients, contractors, and regulatory authorities by visualising the construction process. They can see the project’s progress and upcoming steps.
Also read: Guide to Building Information Modeling (BIM) Impact on Construction Industry
Accurate Prefabrication for Off-Site Construction
The shift toward off-site construction, especially through prefabrication and modular construction, has been greatly supported by BIM.
Off-site construction involves creating building components like walls, floors, and roofing systems in a factory & then transporting them to the construction site. This method offers faster construction times, less on-site labour, and better quality control.
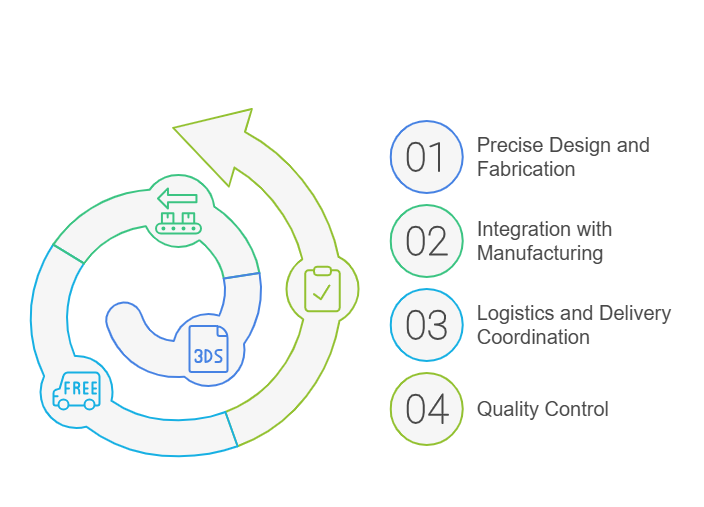
Here’s how BIM plays a crucial role in planning these prefabricated components:
- Precise Design and Fabrication – BIM ensures that the design of prefabricated components is accurate and ready for efficient manufacturing. Detailed 3D models provide exact dimensions, material specifications, and assembly instructions. It ensures that prefabricated components fit perfectly when assembled on-site.
- Integration with Manufacturing – BIM allows smooth coordination between the design team and the off-site manufacturing process. It increases the speed and accuracy of prefabrication while reducing waste and rework.
- Logistics and Delivery Coordination – BIM helps organise the logistics of transporting prefabricated components. It reduces delays caused by poor scheduling or material mismanagement and optimises site operations.
- Quality Control – Prefabricated components made off-site in controlled environments are often of higher quality than on-site construction. BIM ensures that the design and manufacturing processes are closely aligned so all components meet the required specifications and quality standards.
Optimized Site Logistics and Scheduling
BIM’s ability to integrate detailed construction sequencing and material planning also helps improve site logistics and scheduling. Efficient logistics planning, including the management of material deliveries, on-site equipment, and labour, is essential for maintaining a smooth construction timeline.
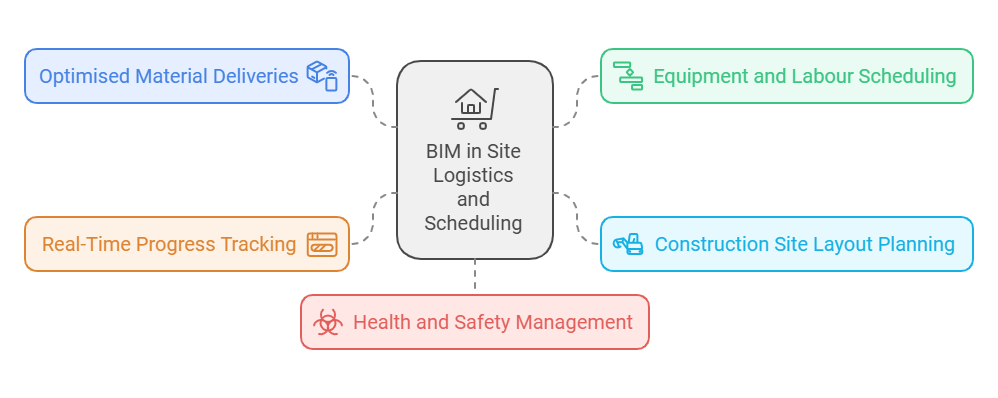
Let’s look at the key benefits of BIM in improving site logistics and scheduling:
- Optimised Material Deliveries – BIM allows for precise tracking of materials and their delivery schedules. Materials can be ordered in the correct quantities and delivered just in time, preventing delays caused by shortages or overstocking. BIM also ensures materials are stored efficiently and easily accessible when required.
- Equipment and Labour Scheduling – BIM helps construction by planning and coordinating equipment and labour use. It ensures workers are assigned to the right tasks at the right times. BIM minimises downtime from waiting for materials, tools, or equipment and boosts productivity.
- Construction Site Layout Planning – BIM enables virtual site logistics planning that allows teams to simulate the layout of the construction site and the flow of activities. It includes planning staging areas, material storage, equipment placement, and worker movement.
- Real-Time Progress Tracking – BIM integrates with project management and scheduling tools that provide real-time updates on construction progress. Any deviations from the planned schedule get identified easily. It allows project managers to take corrective actions before delays grow.
- Health and Safety Management – Efficient site logistics and scheduling also improve safety management. BIM can model construction site activities and workflows to identify potential hazards like traffic congestion, equipment interactions, or worker exposure to dangerous tasks.
Now, let us learn how BIM helps streamline facility management.
Smooth Completion and Facility Management
Building Information Modelling offers tools to streamline facility management, keep accurate digital records, and ensure efficient operations throughout the building’s lifecycle.
With 6D BIM, facilities managers gain access to a detailed digital record of the building. The smooth transfer of data from the construction team to the operations team ensures continuity and helps optimize the building’s performance beyond the construction phase.
Maintaining Comprehensive Digital Documentation
A major benefit of using BIM during the completion phase is the creation of comprehensive digital records that act as a centralised source for all building information.
These records offer detailed data about every aspect of the building, such as structural components, HVAC systems, electrical wiring, plumbing, and finishes.
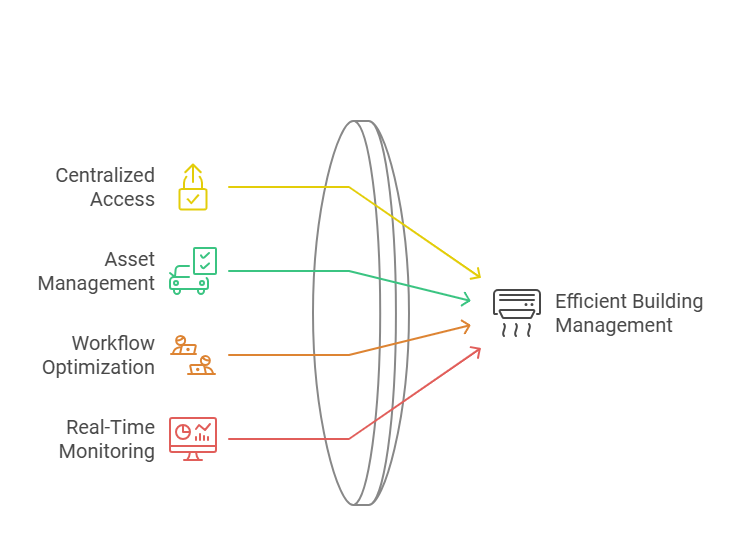
Here are the key advantages of digital records for maintenance and asset management in detail:
- Centralised Access to Information – BIM provides a single, easily accessible database with detailed information about every part of the building. It includes specifications, material types, manufacturer details, maintenance schedules, warranties, and installation dates.
- Efficient Asset Management – Facilities managers can use the BIM model to track the lifecycle of assets and monitor the condition, performance, and age of systems like glass facade sensors, room occupancy sensors, HVAC, lighting, and security. This model helps schedule preventative maintenance, track warranties, and manage service contracts.
- Maintenance Workflow Optimisation – The detailed 3D model helps maintenance personnel quickly locate and access information about systems or equipment requiring attention. It helps plan complex maintenance tasks involving multiple systems, ensuring resources are used efficiently.
- Real-Time Monitoring and Performance Tracking – The BIM model collects real-time data on building performance metrics like energy use, temperature, humidity, and air quality when integrated with IoT sensors. It allows facilities managers to monitor ongoing performance & address potential issues.
Unlocking Benefits of 6D BIM
6D BIM goes beyond the traditional 3D model by incorporating facilities management and operations as an additional dimension. This “sixth dimension” includes data relevant to the building’s ongoing operation and maintenance. It helps facilities managers improve efficiency and sustainability in managing the building throughout its lifecycle.
6D BIM integrates real-time operational data. It enables facilities managers to enhance the performance of building systems like lighting, heating, and cooling. Continuous tracking and adjustments ensure that energy performance remains optimised.
In addition, 6D BIM links maintenance schedules and tasks directly to specific building components. It ensures that facilities managers can track the condition of assets and address issues proactively.
Moreover, 6D BIM collects and records data from design to operation and decommissioning. It provides facilities managers with insights into asset performance and conditions that help them predict when replacements or upgrades are needed.
6D BIM also tracks and optimises sustainability metrics that ensure compliance with environmental standards like LEED or BREEAM. Managers can monitor energy usage, reduce waste, and maintain green building standards.
Ensuring Seamless Project Transition
A key advantage of BIM in facility management is its ability to transition from the construction phase to the operational phase seamlessly. BIM provides a complete, up-to-date digital record that can be easily transferred.
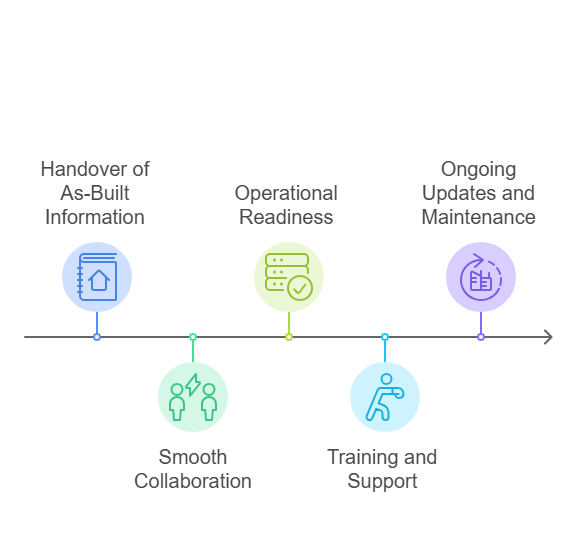
Here are the key factors that facilitate this seamless transition:
- Handover of As-Built Information – At the end of construction, the BIM model gets updated to reflect as-built conditions for incorporating any changes made during the construction phase. Along with the model, key documents like warranties, maintenance schedules, and operation manuals are handed over to support ongoing operations.
- Smooth Collaboration – BIM encourages seamless collaboration between construction and operations teams by providing a shared digital platform. It ensures all stakeholders work from the same accurate model.
- Operational Readiness – Before the building gets occupied, the BIM model can test and verify the performance of key systems, such as HVAC and lighting. Facilities managers can review equipment settings, operational procedures, and performance metrics to ensure everything is ready for daily use.
- Training and Support – The BIM model is valuable for training facility staff. Virtual walkthroughs and simulations help staff understand the building’s systems and components. It enables them to address maintenance tasks effectively and ensure smooth operations.
- Ongoing Updates and Maintenance – You can continuously update the BIM model to reflect any modifications, repairs, or upgrades. It ensures the facilities management team always has access to current and accurate information.
Now, it’s time to discuss how BIM improves project outcomes.
Shaping Construction Industry Standards
BIM drives labour productivity, project efficiency, and cost and time management improvements as construction moves toward more digitally integrated workflows. It also promotes the adoption of advanced technologies, leading to better project outcomes.
Boosting Labor Productivity and Project Efficiency
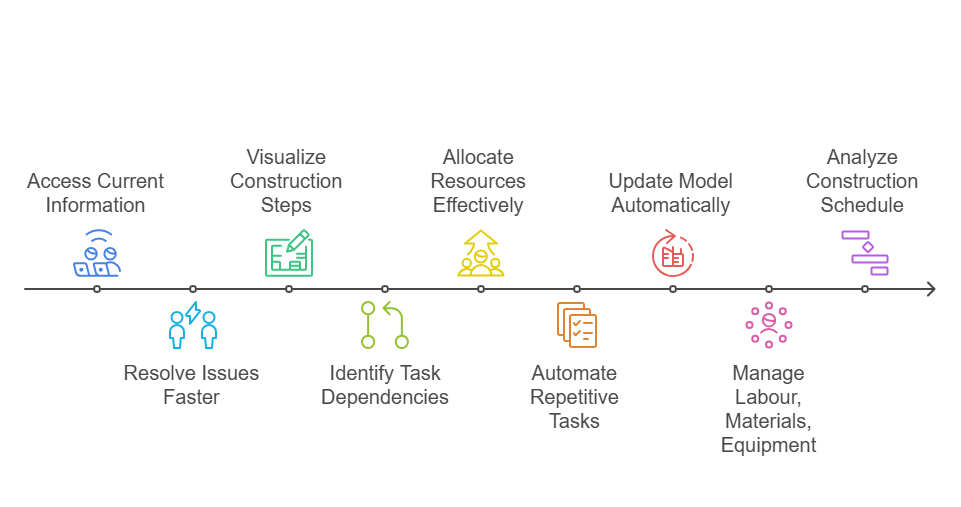
BIM helps construction by boosting labour productivity and improving project efficiency. Teams can access current information, resolve issues faster, track progress, and adjust plans.
Using 4D BIM, teams can visualise construction steps, identify task dependencies, and allocate resources more effectively. It keeps productivity high and reduces idle time. In addition, BIM automates repetitive tasks, such as generating material quantities or producing construction drawings.
When changes are made to one part of the design, the entire model updates automatically and saves time on tasks like estimating material amounts or calculating costs.
Furthermore, BIM tools help manage labour, materials, and equipment more efficiently by tracking their status and availability. By analysing the construction schedule in 4D, project managers can ensure the right number of workers and resources are assigned to tasks at the right time.
Saving Time and Cutting Costs
BIM provides tools to create smooth workflows, reduce inefficiencies, and prevent costly delays. With tools like 4D simulations, teams can foresee scheduling conflicts, adjust task sequences, and ensure all components are on-site when needed. It reduces delays caused by poor planning or logistics, shortening the project timeline.
BIM ensures the right materials are ordered and delivered in the material procurement process. It reduces costs, reduces waste, and improves cost control throughout the project.
In addition, BIM supports 5D BIM, which integrates cost data into the design and scheduling model. It allows for real-time cost estimates and more precise budgeting.
With better coordination and visibility into the project’s needs, BIM helps keep projects moving smoothly without costly interruptions from material shortages or delayed shipments.
Leveraging Digital Tools for Superior Outcomes
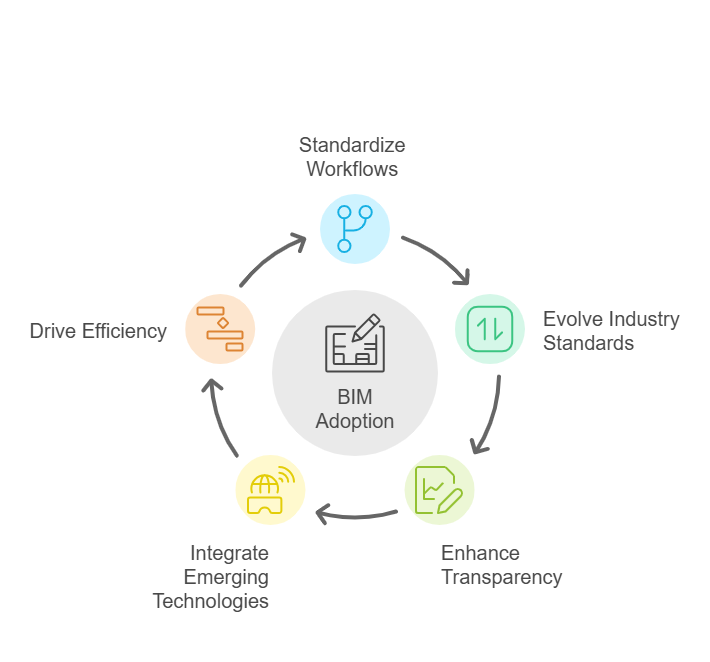
BIM promotes the standardisation of workflows, documentation, and protocols. As more companies adopt BIM, industry standards evolve to support consistent data exchange, model use, and collaboration practices.
Multiple stakeholders can access and modify shared data, improving transparency and alignment. Subcontractors and suppliers benefit from real-time updates that lead to smooth coordination and procurement processes.
BIM is increasingly integrated with emerging technologies like AI, IoT, and AR. IoT sensors. AI can optimise schedules and resource allocation, driving new levels of efficiency, sustainability, and performance in construction.
Now, let’s wrap up with a quick summary.
Conclusion
Building Information Modelling (BIM) is revolutionising the construction industry by bringing unparalleled efficiency, precision, and collaboration to the forefront. By offering a shared digital platform, it empowers architects, engineers, contractors, and stakeholders to work together seamlessly in real time. BIM helps construction, drives smarter decision-making and minimises costly delays.
Teams can visualise detailed, realistic models before construction begins, catch design flaws early and make adjustments with minimal expense and effort. Beyond design, BIM streamlines the management of materials, labour, and equipment, ensuring every resource is utilised to its full potential.
From improving construction timelines and boosting productivity to reducing waste and enhancing sustainability, BIM sets a new benchmark for the industry. It’s not just about creating better buildings—it’s about shaping a future where innovation and sustainability go hand in hand.
Are you looking for BIM solutions?
BIM ASSOCIATES is your one-stop BIM Solution provider for Architecture and Structure. Their solutions help clients with better decision-making, cost-saving, efficient construction planning, and green earth initiatives. GO GREEN.
You might also like: BIM Levels and Stages of Development Explained
FAQs (Frequently Asked Questions)
1. Why is BIM the future of construction?
BIM is the future of construction because it facilitates seamless collaboration between various stakeholders, allowing real-time communication and coordination among project teams.
2. What is the role of BIM in sustainable construction?
BIM allows for sustainable site planning by optimising the orientation of buildings to maximise energy efficiency.
3. How does BIM increase productivity?
BIM increases productivity by neatly organising all the aspects of the project onto a single platform. All construction personnel and project managers can easily view the platform.