Imagine a digital blueprint where every detail, from the initial design to the final touches, is meticulously planned, visualized, and optimized before the first brick is laid. That’s the power of BIM, and it’s at the heart of the UK’s ongoing digital revolution in construction.
But here’s the catch: BIM’s potential can only be fully realized with a clear and comprehensive BIM Execution Plan. It’s not enough to simply implement the technology. You need a proper strategy that aligns teams, streamlines workflows, and ensures every stakeholder is on the same page.
In today’s article, you’ll learn how to execute and implement BIM in your projects. In addition, you will find out the elements of a BIM execution plan and its different types. Let’s start!
Purpose and Importance of a BIM Execution Plan
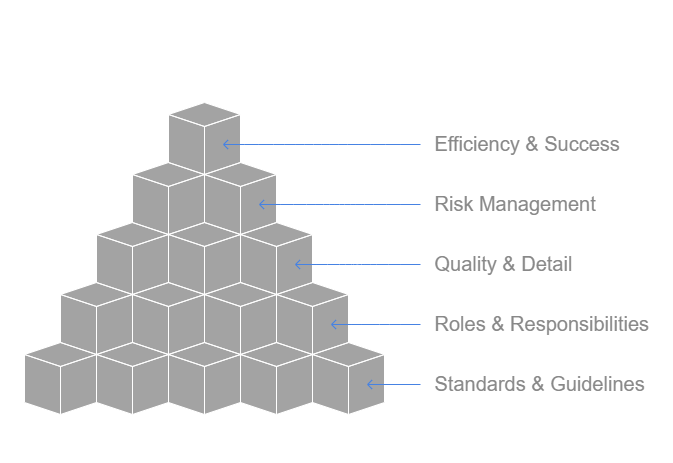
A BIM Execution Plan (BEP) is a document that explains how a BIM project will be carried out, managed, and completed. It helps ensure everyone involved (like architects, engineers, contractors, and owners) understands the project’s goals, timelines, deliverables, and responsibilities. By setting these details at the start, the BEP creates a shared understanding of the project’s objectives and expectations, which helps everyone work together smoothly throughout the project.
The BEP includes industry standards, like ISO 19650, to ensure consistency in processes, modelling rules, data formats, and team collaboration. Following these guidelines helps reduce mistakes and improves the project’s efficiency and data accuracy.
The BEP clearly defines the roles and responsibilities of each team member in the BIM process, from the BIM Manager to the modellers and coordinators. It helps avoid confusion, ensuring that the right people are assigned the right tasks, with clear expectations for managing models, collaborating, and handling data.
The BEP ensures that all outputs meet quality standards by setting expectations for deliverables at each project phase and specifying the Level of Detail (LOD) for models. This standardised approach reduces the need for revisions and rework.
A well-structured BEP helps identify potential risks early, such as problems with model data, miscommunication between teams, or collaboration issues. By setting clear guidelines and regular review points, the BEP reduces costly mistakes and ensures problems are resolved before they grow.
The BEP provides a clear plan for BIM processes, helping avoid mistakes and boosting project efficiency. By creating a predictable and transparent approach to data exchange, model coordination, and project tracking, the BEP helps reduce delays, increase productivity, and lower costs.
Now that we have discussed the purpose and importance of a BEP let’s dive deeper into the key elements of a BIM execution plan.
Key Elements of a BIM Execution Plan
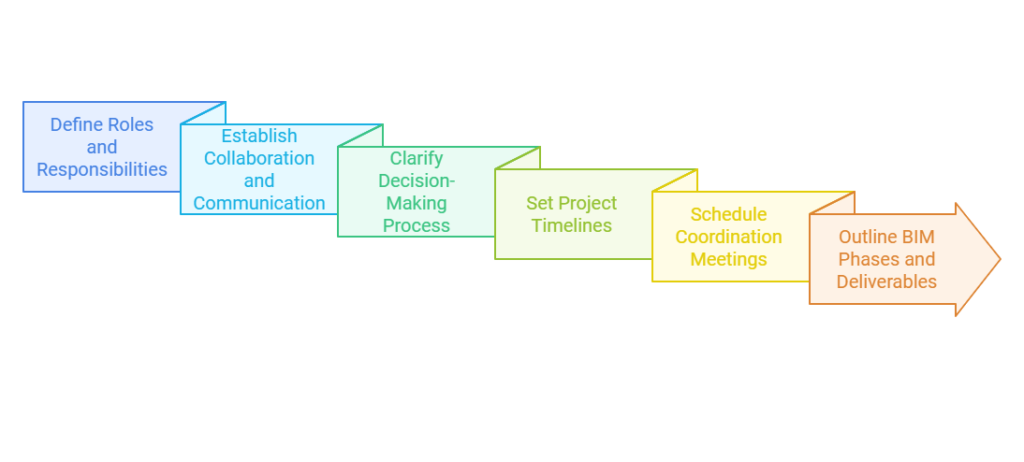
A BIM Execution Plan (BEP) is a crucial document that outlines the strategies, processes, & resources needed for successful BIM implementation in a project. It acts as a roadmap and ensures that all stakeholders are on the same page and that the project runs smoothly and efficiently. Here are the key elements that should be included in a comprehensive BEP.
Roles and Responsibilities
A well-defined BIM Execution Plan specifies the roles & responsibilities of each team member in the project. Each role is assigned specific tasks, such as model creation, quality control, clash detection, data management, and coordination meetings.
Collaboration and Communication
The BEP also sets communication protocols detailing how team members interact and share information. For instance, it may explain how the BIM Manager will coordinate between architecture, structure, and MEP disciplines. Or how the project manager will ensure that BIM requirements align with the overall project goals.
Decision-Making Process
By defining roles, the BEP clarifies who makes decisions about modelling standards, clash resolutions, and revisions. It ensures that decisions are made promptly and efficiently to avoid delays in the project timeline.
Project Timelines
A critical part of the BEP is setting deadlines for model submissions, coordination meetings, clash detection reviews, and other key BIM activities.
Coordination Meetings and Reviews
The BEP should set regular milestones for coordination meetings. The project team should review the current state of the BIM model, address any conflicts or discrepancies, and discuss updates.
BIM Phases and Deliverables
The BEP should outline the specific project phases like schematic design, design development, construction, post-construction and explain how BIM will be used at each stage. For example, during the design phase, the BEP may specify the creation of initial models. Meanwhile, the construction phase may focus on more detailed modelling, scheduling, and cost estimation.
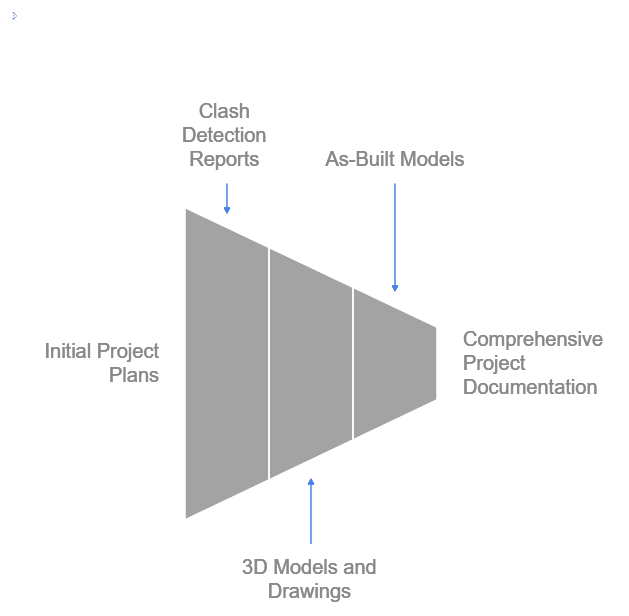
The BEP should specify the deliverables expected at each project phase, ensuring the team knows what to produce and when. These deliverables include:
- Clash Detection Reports – It’s a key deliverable, especially in the early design and construction stages. The BEP should outline the required software, frequency, and format for clash detection and the process for resolving conflicts. The report should highlight design or coordination clashes (e.g., structural vs. MEP clashes), allowing teams to address issues before construction begins.
- 3D Models and Drawings – The BEP defines expectations for the quality, format, and level of detail (LOD) for 3D models at each phase. For example, during schematic design, models may be at a lower LOD (e.g., LOD 100 or 200). Meanwhile, in the construction phase, models may reach higher LODs (e.g., LOD 350, 400 or 500).
- As-Built Models – At the end of the construction phase, the BEP should define the requirements for creating as-built BIM models that reflect the actual construction conditions. These models are valuable for facility management and future renovations.
Besides models and reports, the BEP may include other data-related deliverables, such as cost estimates, material lists, schedules, and energy performance analysis. It should specify the formats and protocols for submitting and storing these deliverables to ensure compatibility and consistency across different teams and tools.
The BEP should also address the final handover of the BIM model to the project owner. It ensures the model is accurate, complete, and ready for facility management. It may include maintenance schedules, equipment manuals, and other assets needed for the building’s operation and upkeep.
Are you looking for 3ds Max-based solutions? BIM ASSOCIATES helps with the 3d modelling of your object, furniture, building, and landscape and helps you create a scenic render and video.
So far, we have discussed the key elements of a BEP. Let’s learn the types of a BIM Execution Plan.
Types of BIM Execution Plans
The BIM Execution Plan (BEP) has two primary types: Pre-contract BEP and Post-contract BEP. Each serves a different purpose and is applied at various stages of the project lifecycle. They ensure BIM processes are well-planned and effectively executed. Let’s get a quick overview of each type.
Pre-Contract BEP: Tendering Stage Plans with Proposed Approaches
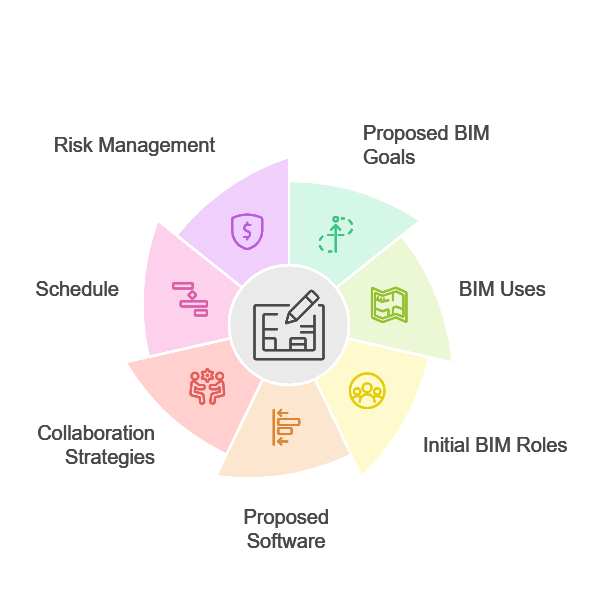
The Pre-contract BIM Execution Plan is created during a project’s tendering or bidding phase before the contract is awarded. It acts as a proposal or strategy that outlines how BIM will be implemented.
The pre-contract BEP helps inform the client and project stakeholders about the bidder’s capabilities and approach to using BIM. Here are the key elements of the Pre-contract BEP:
- Proposed BIM Goals and Objectives – The pre-contract BEP outlines the goals for using BIM on the project, such as improving collaboration, enhancing design accuracy, reducing clashes, or optimising project timelines. These goals are presented to the client to show how BIM will contribute to the project’s success.
- BIM Uses and Applications – This section details the proposed BIM applications or uses (e.g., 3D modelling, clash detection, cost estimation, construction sequencing, and facility management). It highlights how BIM will be applied to improve project outcomes and address specific challenges.
- Initial BIM Roles and Responsibilities – The Pre-contract BEP identifies key personnel responsible for implementing BIM, such as the BIM Manager, BIM Coordinators, and modelling teams. While the roles may be more general at this stage, the document demonstrates the organisational structure needed to support BIM processes.
- Proposed Software and Tools – The Pre-contract BEP outlines the proposed software platforms and tools for BIM. It may also mention file formats and collaboration platforms that will be used for the project.
- Collaboration and Communication Strategies – This section proposes how stakeholders will collaborate using BIM, including data sharing, review, and update methods. It may include approaches for data exchange (e.g., cloud-based platforms, file-sharing protocols) and communication workflows between teams.
- Proposed Schedule and Milestones – The Pre-contract BEP should outline expected BIM-related milestones throughout the project, such as design submissions, model reviews, clash detection, and coordination meetings.
- Risk Management and Contingencies – The Pre-contract BEP identifies potential risks & challenges related to BIM implementation, such as model accuracy, software interoperability, or training needs. The document also outlines strategies to mitigate these risks, showing the bidder’s ability to handle BIM-related challenges.
The Pre-contract BEP gives the client insight into how BIM will be incorporated into the project and reassures them that the team understands BIM processes. It helps identify potential issues, risks, and resource needs early and allows stakeholders to make informed decisions.
The Pre-contract BEP can also be a competitive advantage during the bidding process. It showcases the bidder’s expertise in BIM and commitment to innovation.
Post-Contract BEP: Detailed Task and Schedule Information Post-award
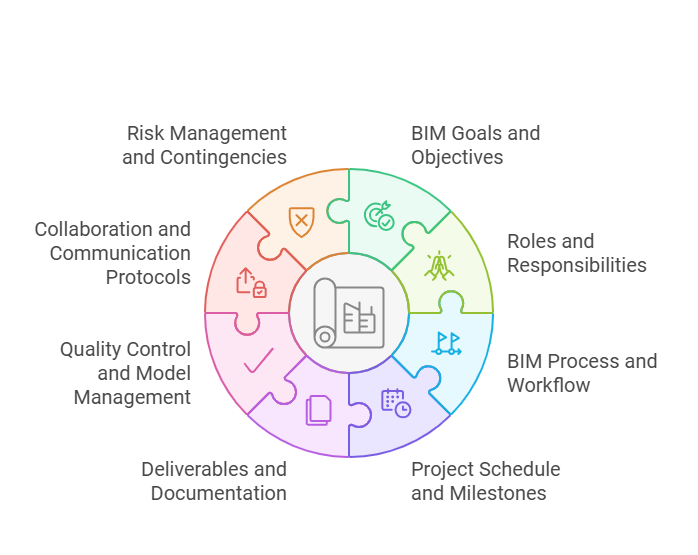
The Post-contract BIM Execution Plan is created after the contract is awarded & the project moves into the design and construction phases. This BEP provides detailed and specific guidelines for how BIM will be executed throughout the rest of the project. It focuses on tasks, scheduling, and resource allocation.
The Post-contract BEP is built on the foundational concepts of the Pre-contract BEP but expands them into a more comprehensive and actionable plan. Here are the key elements of a Post-contract BEP:
- Detailed BIM Goals and Objectives – While the Pre-contract BEP may propose general goals, the Post-contract BEP outlines clear, detailed objectives for each phase of the project. These objectives include deliverables, milestones, and expected outcomes for BIM applications at various stages (e.g., coordination, construction sequencing, etc.).
- Roles and Responsibilities – The Post-contract BEP clarifies and formalises the roles and responsibilities of each team member. It specifies who will manage BIM, perform quality control checks, and be responsible for model updates, revisions, and collaboration. This section ensures all tasks are assigned effectively, with clear accountability for each role.
- Detailed BIM Process and Workflow – The BEP outlines step-by-step processes for creating, reviewing, and updating BIM models. It includes timelines, responsibilities for each process, and checks or validations before model delivery. This section provides a clear workflow for how BIM will be used through the design, construction, and post-construction phases. It includes how and when models will be updated, reviewed, and coordinated.
- Project Schedule and Milestones – The Post-contract BEP provides a detailed project schedule, incorporating BIM-specific milestones such as initial model creation, clash detection, and resolution meetings. It also includes BIM reviews, coordination sessions, and final model delivery (including as-built models). These milestones align with the project timeline to ensure BIM activities match construction schedules.
- Detailed Deliverables and Documentation – This section specifies the detailed BIM deliverables at each stage. It includes 3D models, clash detection reports, quantity take-offs, cost estimates, construction sequencing, and as-built models for facilities management. It also outlines the formats and protocols for submitting these deliverables, ensuring consistency and quality across the project.
- Quality Control and Model Management – The Post-contract BEP includes detailed procedures for managing model quality, including handling revisions, clash detection, and coordination issues. It sets standards for model accuracy, file naming conventions, and data management practices, ensuring consistency and reliability throughout the project lifecycle.
- Collaboration and Communication Protocols – As the project progresses, the BEP outlines how teams will collaborate on BIM, detailing regular coordination meetings, digital collaboration tools, and document control systems. This section ensures efficient information flow between teams, keeping all stakeholders updated on the model’s status and addressing any issues.
- Risk Management and Contingencies – The Post-contract BEP further refines risk management strategies identified in the Pre-contract BEP, focusing on challenges encountered during project execution. It includes contingency plans for technical issues, model errors, or delays in the BIM process, ensuring the project stays on track.
The Post-contract BEP ensures that all BIM activities align with the project’s objectives and timelines.
Also read: BIM Levels and Stages of Development Explained
Now that you know the types of BPE, let’s move ahead and discuss how to develop a BIM Execution Plan.
Steps for Developing a BIM Execution Plan
Research says that over 70% of UK construction professionals have implemented BIM software into their programmes. BIM is set to revolutionise the whole building and construction sectors, and as a global leader in the adoption of BIM, the UK is at the forefront of this revolution.
As the country continues to lead this digital shift, professionals must develop a comprehensive and effective BIM Execution Plan (BEP) to leverage the benefits of this technology. Let us look at the following steps for developing a comprehensive & effective BEP.
Step 1. Identifying Goals and Objectives
The first step in developing a BEP is identifying the specific goals for using BIM in the project. These goals should align with the overall project objectives, such as improving design accuracy, reducing rework, enhancing collaboration, or optimising project delivery times.
The typical BIM goals might include:
- Improved scheduling (4D) to synchronise construction activities with project timelines.
- Clash detection and resolution to prevent costly design errors.
- Facility management by providing as-built models for easier maintenance and future renovations.
- Cost estimation (5D) to monitor budget and material costs in real time.
The BEP should translate these broad goals into specific, measurable objectives that can be tracked throughout the project. For example:
- Completing the model to LOD (Level of Development) 400 by the end of the design phase.
- Achieving a 90% reduction in design-related clashes before construction begins.
- Ensuring that the BIM model is updated weekly to reflect construction progress.
Ensure the BIM goals and objectives align with the project owner’s expectations, key stakeholders, and the project team. This may involve consultations with owners or operators to understand how the BIM model will support facility management after construction.
Step 2. Understanding Team Hierarchy and Scope
Understanding the project hierarchy and the scope of work is essential for aligning BIM activities with the overall project structure. This includes:
- Project stages (e.g., concept, design, construction, post-construction).
- Key disciplines involved include architecture, structural engineering, MEP (Mechanical, Electrical, Plumbing), and civil engineering.
- External stakeholders like subcontractors, suppliers, and the project owner will interact with the BIM process.
Clearly define where and how BIM will be used in each project phase:
- Design Phase – Development of initial 3D models, clash detection, and design reviews.
- Construction Phase – Coordination of construction schedules (4D), material take-offs, and real-time model updates.
- Operation Phase – Handover of as-built BIM models for use in facilities management.
Understand how the different teams and disciplines will need to collaborate using BIM. This involves specifying model coordination, data exchange protocols, and collaborative workflows.
For instance, MEP systems may need to be coordinated with structural elements to avoid clashes, and regular review sessions will be necessary to ensure alignment.
Step 3. Assignment of Roles and Accountability
A successful BEP clearly outlines the roles and responsibilities of each team member involved in BIM implementation. These roles should align with the project’s scope and objectives. Common BIM roles include:
- BIM Manager – Oversees the entire BIM process, ensuring standards and procedures are followed. Responsible for the overall execution and quality control of the BIM process.
- BIM Coordinator – Works closely with the BIM Manager to coordinate the development and integration of models across different disciplines. Ensures model compatibility and resolves coordination issues.
- BIM Modellers – Create and update the 3D models according to established standards and specifications.
- Project Managers and Engineers – Ensure that BIM supports project goals such as cost estimation, scheduling, and field operations.
The BEP should specify who is responsible for creating, reviewing, and updating deliverables throughout the project. For example:
- Clash detection reports should be the responsibility of the BIM Coordinator, but the BIM Manager must sign off on them.
- The BIM Modellers should manage model updates with the project’s design changes.
- The BIM team must deliver final as-built models at the end of construction, but accountability may shift to the contractor or owner’s facilities management team for post-construction updates.
The BEP should outline communication protocols to ensure accountability. This includes regular review meetings to track progress, discuss challenges, and resolve issues. This also includes documented processes for handling changes or problems with the model, ensuring that the right people are involved in decision-making.
As we have discussed the development phase, let’s move on to the execution strategy.
Execution Strategy
The Execution Strategy of a BEP outlines the methods and frameworks that will guide the use of Building Information Modelling (BIM) throughout the project lifecycle.
It ensures the project’s BIM objectives are structured and systematic, with the necessary tools, resources, and priorities defined upfront. Here are the key components of the Execution Strategy:
- Establishing Framework Priorities and Objectives
Initially, the project’s BIM execution strategy should set important priorities that match the project’s needs and the overall goals of using BIM. These priorities will guide all the steps that follow. For example:
- Collaboration and Coordination – Make sure that teams from different disciplines (architecture, engineering, construction, etc.) can work together smoothly, with real-time access to a shared BIM model.
- Clash Detection and Conflict Resolution – Focus on spotting and solving design and construction issues early through clash detection and virtual model reviews.
- Time and Cost Management – Use 4D and 5D BIM to improve scheduling (4D) and cost estimation (5D), helping track construction progress, predict delays, and manage project budgets.
- Data Integrity and Quality – Ensure high-quality, accurate data throughout the BIM process to create reliable models and prevent rework or construction mistakes.
- Sustainability and Performance – Use BIM tools for energy performance modelling, sustainability analysis, and environmental impact assessments to support energy-efficient building design and operations.
Establish measurable objectives for the BIM process that align with the project’s overall goals. Examples of specific BIM objectives could include:
- Achieving 95% accuracy in clash detection reports before construction.
- Reducing the construction schedule by 10% using 4D simulation and sequencing.
- Delivering an as-built BIM model for facilities management purposes within 30 days of project completion.
Define milestones that mark key stages of BIM implementation, such as model review deadlines, clash detection milestones, or the handover of as-built models. Set Key Performance Indicators (KPIs) to track progress toward meeting BIM objectives, ensuring that all stakeholders know their targets and responsibilities.
- Personnel and Software Requirements
The execution strategy should define the human resources needed to implement the BIM plan effectively. It includes:
- BIM Manager: Oversees the entire BIM process, ensures adherence to standards, manages workflows, and resolves issues.
- BIM Coordinators: Integrate models across disciplines, handle model reviews, and manage the clash detection process.
- BIM Modellers: Create and update 3D models based on the project design and collaborate with the relevant stakeholders.
- Project Managers, Engineers, and Architects: Work together on BIM-related tasks such as design reviews, scheduling, cost estimation, and quality assurance.
- IT and Technical Support: Ensure proper installation, setup, and maintenance of BIM software and hardware systems.
Ensure the team has the right technical skills and experience to use BIM tools effectively. It includes knowing how to use specific BIM software (like Revit or Navisworks), understanding project management methods (like 4D and 5D BIM), and following BIM standards (such as ISO 19650).
The strategy should also include plans for ongoing training so the team stays updated with the latest BIM technologies, methods, and software updates.
- Selection of Key Software Tools
Choose the right software tools based on the project’s needs and BIM goals. Consider the size, complexity, and desired outcomes when selecting the software used throughout the project.
Core BIM Software for Model Creation and Collaboration
For Modelling software, choose tools to create detailed 3D models, such as:
- Revit for architectural, structural, and MEP design.
- Tekla Structures for Structural Steel Modelling.
- ArchiCAD for architectural design.
For Coordination and Clash Detection software, choose tools for identifying and resolving conflicts in models:
- Navisworks for clash detection and model coordination.
- Solibri Model Checker for model validation and quality control.
For Collaboration platforms to facilitate team communication and data sharing:
- BIM 360 or Procore for cloud-based collaboration and document management.
- Trimble Connect or Aconex is used to manage construction workflows.
Software for Specific BIM Uses
- 4D Scheduling and Construction Simulation – Tools like Synchro or Navisworks Manage help with construction sequencing and integrating schedules.
- 5D Cost Estimation – Software like Vico Office or CostX for real-time cost tracking linked to the BIM model.
- Energy Performance and Sustainability Analysis – Tools like IESVE, EnergyPlus, or Green Building Studio for environmental and energy modelling.
Ensure that the chosen software tools can work together smoothly by being compatible. The execution plan should outline how different file formats (e.g., IFC, Revit files, DWG) can be shared and integrated across various tools.
Now, it’s time to discuss the implementation of the BIM Execution Plan and how to maintain the quality of the project.
Implementation and Quality Control
A BIM Execution Plan (BEP) is a roadmap for integrating Building Information Modelling (BIM) into every project phase. If you want to ensure the project is finished on time, within budget, & meets quality standards, the BEP should include clear timelines and quality control processes.
These processes ensure the BIM model stays accurate and consistent throughout the project. This section will explain how to develop timelines, distinguish between quality assurance & quality control, and why keeping the BEP updated throughout the project is essential.
Timeline Development with Milestones
A well-defined timeline with clear milestones is crucial for successfully executing BIM. The timeline tracks the project’s progress and ensures that BIM deliverables are met on schedule.
To create a successful timeline for BIM activities, it’s essential to identify key milestones tied to specific project phases. These milestones ensure that the BIM process aligns with the project schedule. Here are some examples of BIM-related milestones for each phase:
Design Phase Milestones:
- Initial BIM model submission (e.g., preliminary architectural models, MEP coordination).
- Clash detection and resolution reports.
- Mid-design model review and coordination meeting.
Construction Phase Milestones:
- Weekly or bi-weekly updates of BIM models to reflect changes in the field.
- Detailed 4D BIM construction sequencing (scheduling with 3D models).
- Monthly coordination meetings and clash resolution updates.
Post-Construction Milestones:
- Final as-built BIM model delivery for facilities management.
- Completion of model handover, including operation manuals and maintenance schedules.
These milestones help keep the BIM process on track & ensure that all stakeholders are aligned with the evolving model and project goals. It will help ensure that BIM tasks like model creation, clash detection, and coordination stay on track without causing delays or disruptions. Tools like Primavera or Microsoft Project effectively merge BIM milestones with the project plan.
Establishing a process for regularly reviewing the BIM timeline is also essential. This includes monitoring key activities like model creation, coordination, and clash detection. Holding weekly or bi-weekly check-ins allows the team to stay updated on progress & make adjustments as needed.
Since BIM processes often reveal unexpected challenges, such as clashes or design changes, it’s wise to include buffer time in the schedule. Contingency periods offer flexibility to address these issues without impacting the project timeline. This approach ensures that the BIM process can adapt while keeping the project on schedule.
Quality Assurance vs. Quality Control in BIM
Quality Assurance (QA) & Quality Control (QC) are crucial for ensuring that BIM models and data are accurate and reliable, but they serve different purposes. Quality Assurance (QA) is a proactive approach. It involves setting up processes, standards, and guidelines to ensure BIM workflows are consistent and follow best practices throughout the project. QA aims to prevent errors by establishing a framework for quality from the start. A platform like Plannerly is a great tool for quality control.
On the other hand, Quality Control (QC) is a reactive approach. It reviews and tests BIM models to identify and correct errors or inconsistencies. QC ensures the final model meets quality standards by addressing issues like clashes, missing details, or design mistakes.
Let’s understand this comparison below:
Aspects | Quality Assurance (QA) | Quality Control (QC) |
Focus | Improving processes & procedures. | Inspecting final outputs for defects. |
Goal | To prevent defects by adhering to set standards, methods, & best practices. | To detect & fix defects in BIM models before project delivery. |
Scope | Broad consists of the entire BIM workflow, including planning, design, and execution. | Narrower focuses specifically on the finished product or model. |
Methods | Process audits, training, process standardization, & documentation reviews. | Model reviews, clash detection, & final inspections of BIM outputs. |
Timing | Implemented throughout the project lifecycle. | Applied towards the end of the project to check for errors in the final model. |
Outcome | Improved processes & adherence to best practices in future BIM projects. | A refined, defect-free BIM model ready for construction or delivery. |
5 Tips for Enhancing BIM Implementation
Successful BIM implementation requires careful planning and the adoption of best practices throughout the project lifecycle. You can optimize your approach and achieve maximum efficiency by following key strategies. Here are five tips for enhancing BIM implementation to ensure your project stays on track and delivers superior results.
- Create a Centralized Data System – Set up a cloud-based platform where everyone involved in the project can access, update, and share BIM models and data in real-time. Use tools to manage this data to ensure everyone is on the same page and reduce mistakes caused by poor communication.
- Use AI and Machine Learning – Go beyond basic modelling by adding AI-driven analytics. By looking at past project data, AI can predict potential issues like design clashes, material shortages, or scheduling problems before they happen. It can also help improve the construction timeline and resource management.
- Build Custom Templates and Standards – Create templates and standards that fit the specific needs of your projects and team. For example, set up custom rules for naming, modelling parameters, and layer definitions to match your team’s work style and goals.
- Implement a Digital Twin Strategy – A digital twin is a virtual copy of the building or structure. It can be useful for managing and maintaining the building after construction. It also provides insights into its performance and helps with upkeep. Think about how you can include digital twins in your BIM process.
- Encourage Ongoing BIM Learning – Promote continuous learning about BIM within your organization. This could involve regular training, sharing knowledge within the team, or attending industry events. Encourage your team to keep up with the latest BIM tools, trends, and updates.
Now, as we have discussed everything about the BIM Execution Plan and its implementation, so let’s wrap up with a quick summary.
Conclusion
Implementing a BIM Plan is a strategic move that can elevate your construction projects’ efficiency, collaboration, and quality. From setting objectives to defining roles, managing workflows, and maintaining quality control, each step plays a crucial role in the success of your project.
Remember, BIM implementation is not a one-time task but an ongoing improvement process. You’ll ensure your projects are delivered on time by continuously refining your BIM strategies and staying up-to-date with the latest tools and practises. Also, your projects will be within budget and exceed the expectations of clients and stakeholders.
Are you looking for BIM solutions?
BIM ASSOCIATES is your one-stop BIM Solution provider for Architecture and Structure. Their solutions help clients with better decision-making, cost-saving, efficient construction planning, and green earth initiatives.
You might also like: Guide to Building Information Modelling (BIM) Impact on Construction Industry
FAQs (Frequently Asked Questions)
- Who prepares the BIM execution plan?
The project team collaboratively develops the BIM Execution Plan (BEP) at various stages. This process involves input from key stakeholders, including architects, engineers, contractors, and BIM managers, to ensure alignment with project goals.
- What is the post-BIM execution plan?
The Post-contract BEP builds on the Pre-contract BEP by finalising critical details such as model management protocols, data exchange methods, and quality control processes. It is a detailed guide for BIM implementation during the project’s design, construction, and operation phases.
- What is the difference between a BIM implementation plan and a BIM execution plan?
The BIM Implementation Plan (BIP) provides a broad framework for adopting BIM across an organization or department, focusing on overall strategies, training, and resource allocation. The BIM Execution Plan (BEP) is project-specific, detailing the tactical and procedural aspects of implementing BIM for a particular project.