The Bill of Quantities (BOQ) is a vital tool in the construction industry, offering a detailed breakdown of materials, labour, and costs needed for a project. Its importance becomes even more evident when considering that nearly 85% of construction projects face cost overruns.
By breaking the work into clear, measurable sections, the BOQ helps contractors submit competitive bids and supports project owners in keeping their budgets on track. Whether you’re a contractor, quantity surveyor, or project owner, a well-prepared BOQ helps simplify communication and reduce disputes, making it a key part of any successful construction project.
In this article, you’ll understand the meaning of BOQ, its types, the creation process, and how to avoid common mistakes that could impact your project.
What is the BOQ (Bill of Quantities)?
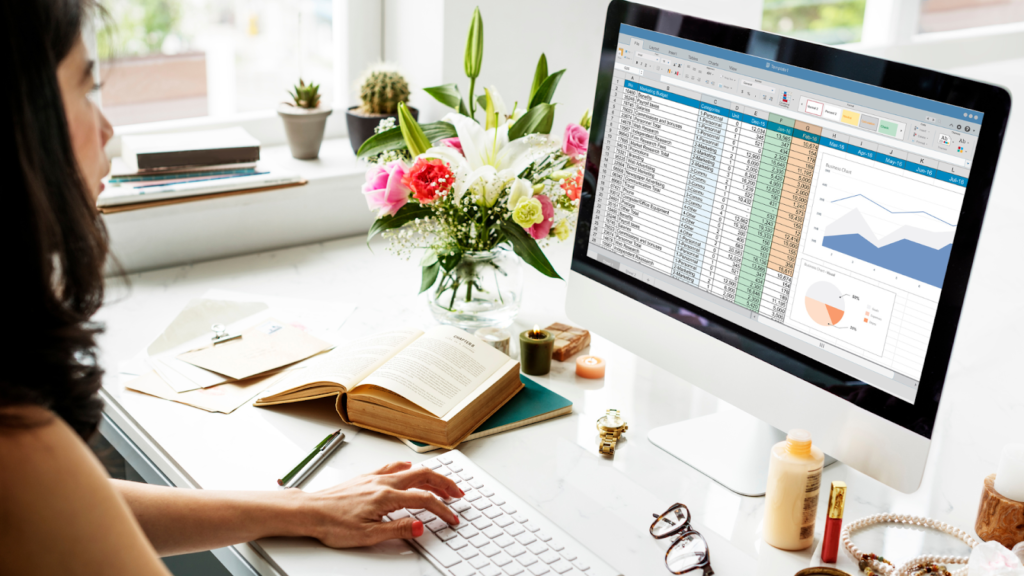
The Bill of Quantities (BOQ) is a detailed document that lists all materials, count, type, , and costs needed for a project. It is a standard tool for cost estimation, tendering, and contract management.
The BOQ defines the project scope with precise, quantifiable details, including each task’s specifications, unit measurements, and pricing. It breaks down costs and quantities to ensure transparency, helps with accurate budgeting, and allows contractors to submit competitive bids.
The BOQ also serves as a reference for tracking progress, controlling costs, and managing changes throughout the project. Its flexibility shows how it can be used at different project stages. For example, the Approximate Bill of Quantities is invaluable in the early planning stages, as it gives a rough idea of costs before they are fully defined.
Use of Approximate Bill of Quantities (BOQ)
An Approximate Bill of Quantities (BOQ) is used when a detailed BOQ cannot be prepared during tendering, such as when the design is mostly complete but exact quantities are still unknown. However, this approach may lead to more variations during construction, resulting in less price certainty when making the investment decision.
Some contracts allow for the re-measurement of approximate quantities, such as in roadworks for cut and fill. In these cases, quantities are adjusted, and payments are made accordingly without issuing a variation.
If an approximate quantity is unrealistic compared to the actual amount needed, it could lead to a relevant event. This may result in claims for an extension of time and additional costs.
This highlights the importance of accuracy in project planning and cost estimation. In design-bid-build projects, the Bill of Quantities (BOQ) is crucial in connecting the design and construction phases, ensuring clear communication and alignment among all parties involved.
Role of the BOQ in Design-Bid-Build Projects
The Bill of Quantities (BOQ) is a key element in the design-bid-build project model, which divides the project into design, bidding, and construction phases. The BOQ connects the design and bidding stages, ensuring all stakeholders—owners, contractors, and consultants—understand the project scope.
In design-bid-build projects, the Bill of Quantities (BOQ) is typically included in the bidding package for contractors. Since the BOQ already lists predefined materials and quantities, contractors can bypass their quantity takeoff and use the BOQ directly for pricing.
The BOQ helps in design-bid-build projects in the following ways:
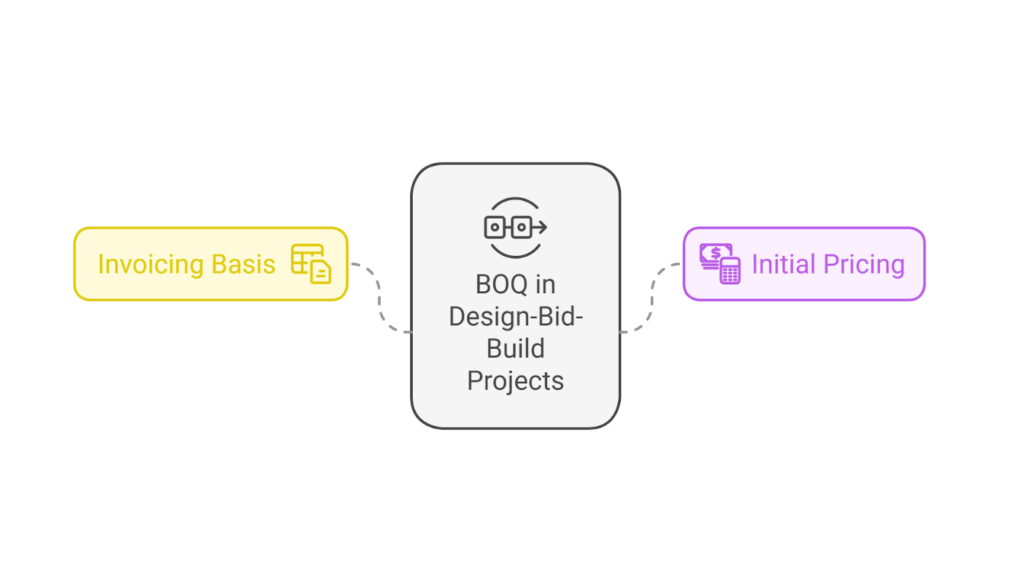
- BOQ as Invoicing Basis: Once a contractor is selected, the BOQ serves as the schedule of values for invoicing throughout the project. This allows for easy progress tracking by comparing the quantities of materials delivered and work completed with the BOQ quantities.
- Approximate BOQ for Initial Pricing: When the design is not finalised during the bidding phase, an approximate BOQ provides initial quantity estimates for pricing. Once the design is completed, these amounts can be updated later to reflect the final quantities.
This dual purpose shows how important the BOQ is for keeping things transparent, accurate, and efficient throughout the project. Understanding what the Bill of Quantities (BOQ) includes helps clarify its structure and purpose.
What Does the Bill of Quantities Include?
The Bill of Quantities (BOQ) breaks down materials, tasks, labour, and costs, offering a clear and organised view of the project’s requirements. Knowing the components of a BOQ is essential for ensuring transparency, reducing disputes, and controlling the construction process. The Bill of Quantities includes:
Sections | Key Details |
Item Descriptions | Detailed descriptions of work items, including materials, tasks, and specifications. |
Units of Measurement | Standard units for each item (e.g., cubic metres, square metres, kilogrammes, pieces). |
Quantities | Precise amounts of materials and labour required for each task, based on project drawings and specifications. |
Rates | Unit rates for materials, labour, and equipment, accounting for overheads and profit margins. |
Total Costs | Calculated costs for each item, derived by multiplying quantities by rates. |
Work Categories | Logical sections for grouping items include foundations, superstructure, finishes, and MEPF installations. |
Provisional Sums | Allowances for undefined tasks or materials are indicated as provisional items. |
Contingencies | Allocated costs for unforeseen expenses or variations in the project. |
Special Instructions | Notes or guidelines for contractors, such as quality standards or specific requirements. |
Summary | Overall cost breakdown, including subtotal for each category and total project cost. |
A Bill of Quantities (BOQ) outlines the materials, labour, and costs involved in a construction project, ensuring accurate budgeting and resource planning. While it plays a key role in cost estimation, it’s often compared to another essential document—the Bill of Materials (BOM).
Bill of Quantities vs Bill of Materials
The Bill of Quantities (BOQ) and the Bill of Materials (BOM) are both key documents in construction, but they serve different purposes and audiences. Understanding how they differ is essential for effective project planning, helping to control costs and ensure materials are available when needed throughout the construction process.
Below are the key differences between the Bill of Quantities and the Bill of Materials:
Aspects | Bill of Quantities (BOQ) | Bill of Materials (BOM) |
Definition | A detailed breakdown of materials, labor, work required, and associated costs for a construction project. | A complete list of raw materials, components, & parts needed for construction or manufacturing. |
Purpose | Used for cost estimation, tendering, and contract management in construction projects. | Used to organise material procurement and ensure availability for construction. |
Scope | Includes materials, labour, equipment, and associated costs. | Focuses only on materials and their specifications. |
Audience | Primarily for quantity surveyors, project owners, and contractors. | Primarily for procurement teams, warehouse managers, and suppliers. |
Preparation | Prepared by quantity surveyors based on project drawings and specifications. | Prepared by engineers or procurement teams based on design specifications. |
Details Provided | Item descriptions, unit measurements, quantities, rates, and total costs. | Material names, quantities, part numbers, and specifications. |
Use Case | Serves as a tool for bidding, payment tracking, and project progress monitoring. | Helps with inventory planning, ordering, and production schedules. |
Relation to Project Stages | Linked to tendering, budgeting, and execution stages. | Linked to procurement and supply chain stages. |
Inclusion of Labour Costs | Includes labour and associated costs alongside materials. | Excludes labour costs; focuses solely on materials. |
Format | Structured into sections for each part of the construction project (e.g., foundation, finishes). | Structured into a list or hierarchical format for easy material tracking. |
Relevance | Essential for contract management and financial transparency. | Essential for material planning and avoiding supply chain disruptions. |
While the differences between the Bill of Quantities (BOQ) and the Bill of Materials (BOM) highlight their unique roles, the BOQ stands out for its comprehensive approach to managing construction costs and processes.
Primary Purpose of Bill of Quantities
The main purpose of the Bill of Quantities (BOQ) is to list and quantify all materials, labour, and tasks needed to complete a construction project, ensuring accurate cost estimation. It is a standard reference for project owners, contractors, and consultants to compete fairly during bidding and support effective cost management throughout the construction process.
The primary purposes of the Bill of Quantities are:
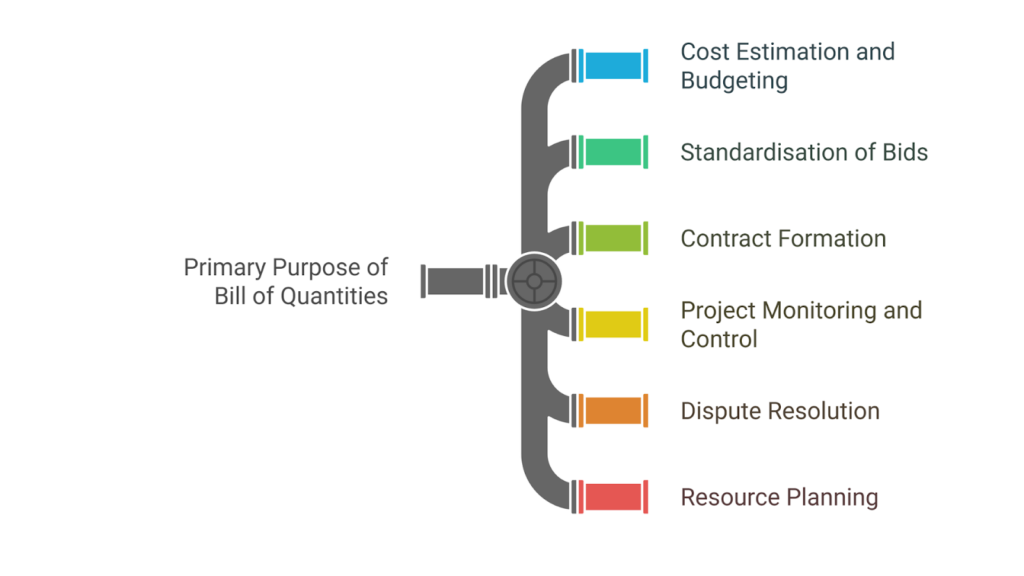
- Cost Estimation and Budgeting: Help owners estimate the total project cost accurately. Provide a detailed breakdown of quantities and rates for effective budget allocation and reduce financial surprises during execution.
- Standardisation of Bids: Ensures contractors prepare their bids on the exact specifications and quantities during tendering.
- Contract Formation: Acts as a reference for scope, quantities, and costs. Defines the responsibilities of all parties and ensures clear communication throughout the project’s lifecycle.
- Project Monitoring and Control: Tracks project progress and manages changes. Helps monitor costs, spot any overruns, and address any issues quickly.
- Dispute Resolution: Offers a clear and structured framework for resolving disputes in case of disagreements regarding payments, variations, or scope changes.
- Resource Planning: Outlines materials and tasks, helping contractors plan procurement, labour, and equipment more efficiently. Ensures that the project is completed on time and executed smoothly.
Once you understand the primary purpose of the Bill of Quantities (BOQ), it’s easier to see how different types are used at various stages of a project to meet specific needs and requirements.
Ready to simplify your projects and experience these benefits firsthand?
BIM ASSOCIATES is your one-stop BIM Solution provider for Revit Architectural and Structural Solutions. They coordinate with your team to develop, record, and streamline the BIM Revit Model, along with the sheets, Bill of Quantities, Bill of Materials, and clash coordination.
Types of Bill of Quantities
The Bill of Quantities (BOQ) is tailored to meet the specific needs of different project stages and stakeholders. The types of BOQ vary based on the stage of the project and the level of detail required. Understanding the key types of BOQs helps stakeholders select the right approach for their project’s needs.
Below are the main types of Bill of Quantities in construction:
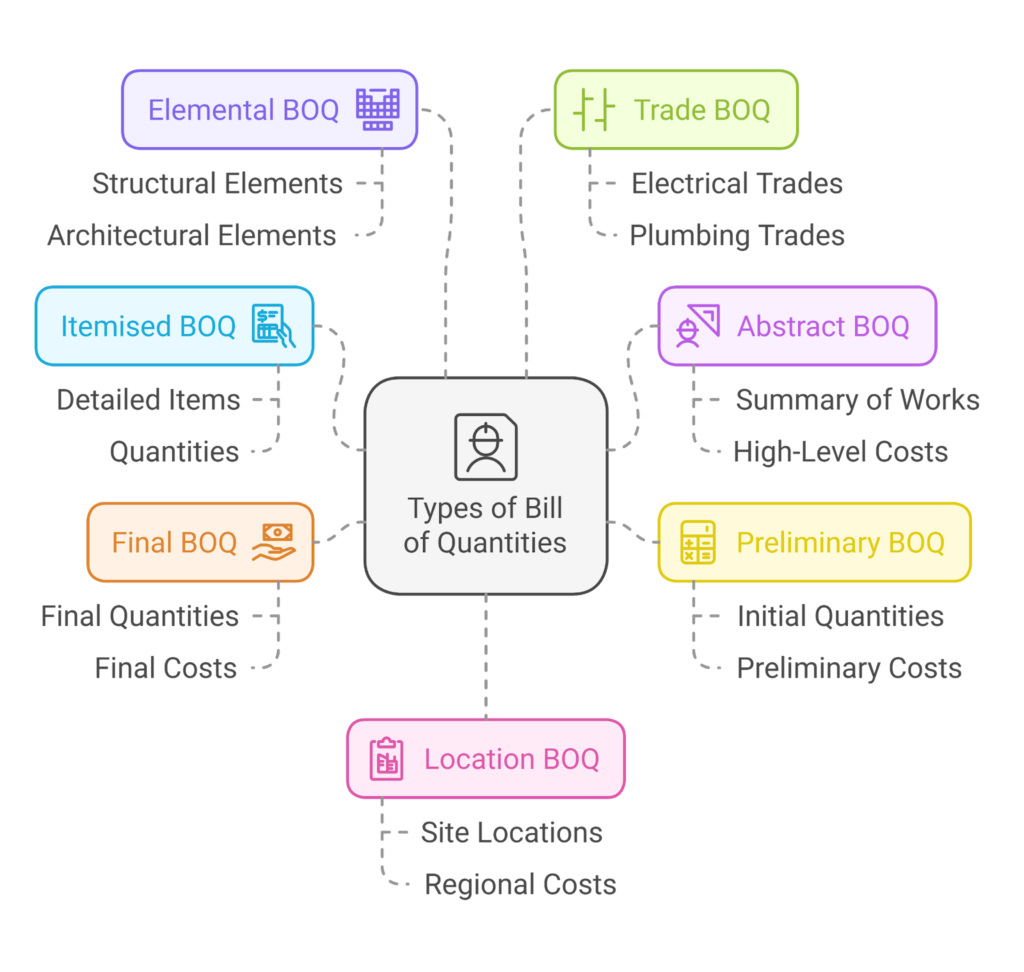
Types of BOQ | Key Details | Use Cases |
Itemised BOQ | A detailed list of all materials, labour, and tasks, including quantities and rates. | Large-scale projects that require accuracy and detailed breakdowns. |
Abstract BOQ | A summary BOQ with key items and approximate quantities. | Early project stages for cost overviews. |
Preliminary BOQ | An approximate BOQ based on incomplete designs or initial project information. | Early planning and decision-making phases. |
Final BOQ | A complete BOQ prepared from finalised project designs and specifications. | Execution and tendering stages where finalised costs are critical. |
Elemental BOQ | Organised by functional elements of the project, such as foundation, walls, etc. | High-level cost comparisons and project element assessments. |
Trade BOQ | Categorised by construction trades, such as plumbing or electrical. | Projects with multiple specialised subcontractors. |
Location BOQ | Divided by project locations or areas, specifying quantities and costs for each. | Complex projects requiring location-specific cost tracking and planning. |
Understanding the main purpose of the Bill of Quantities (BOQ) highlights its crucial role in construction projects. However, to ensure accuracy, consistency, and transparency, BOQS must follow established standards.
Also read: UK BIM Level 2 Deliverables: Details, Benefits & Future.
Standards for Bills of Quantities
In the UK, Bills of Quantities (BOQs) are prepared following established standards to ensure consistency, accuracy, and clarity in construction projects. These standards are widely recognised and used by construction industry professionals.
The standards for Bills of Quantities are as follows:
- NRM2 (New Rules of Measurement 2): This UK standard was developed by the Royal Institution of Chartered Surveyors (RICS) for preparing BOQs in construction projects. It provides guidance on listing and quantifying materials, labour, and costs for accurate tendering and contract management.
- Civil Engineering Standard Method of Measurement (CESMM4): This was created by the Institution of Civil Engineers (ICE) and provides specialised guidelines for earthworks and infrastructure projects.
- RIBA Plan of Work: This framework aligns BOQ preparation with different project stages, ensuring it fits smoothly into the project lifecycle.
Adhering to established standards ensures consistency and reliability in preparing a Bill of Quantities (BOQ). Building on these guidelines, the next step is understanding how to create an accurate BOQ.
Creating an Accurate Bill of Quantities
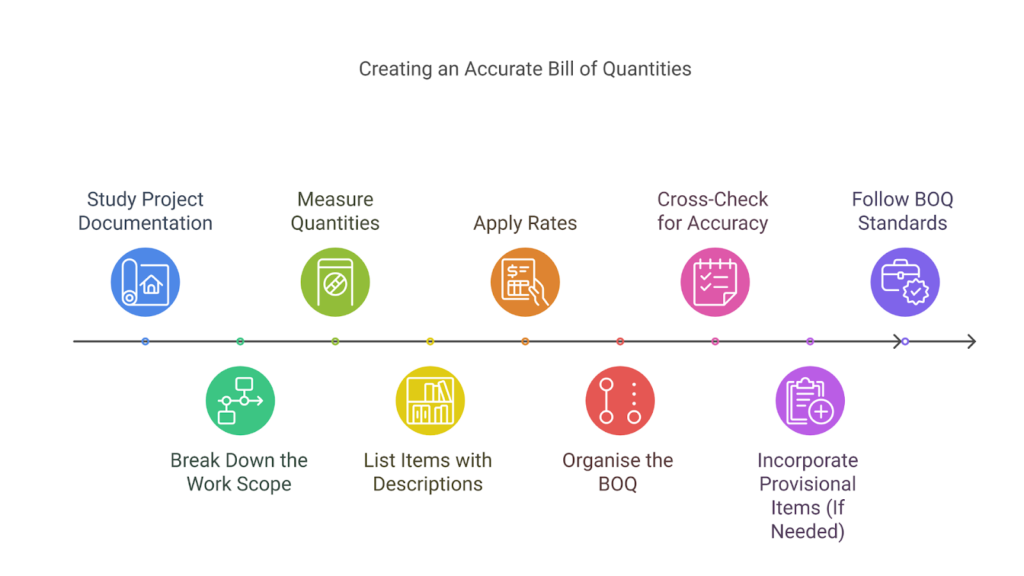
Creating an accurate Bill of Quantities (BOQ) is key to successful construction project management. When the BOQ is prepared accurately, it helps reduce the risk of disputes, cost overruns, and resource mismanagement, making it an essential tool for everyone involved in the project.
An accurate BOQ demands careful attention to detail, a structured approach, and adherence to established standards such as the New Rules of Measurement (NRM2).
Here are the steps to create an Accurate Bill of Quantities:
- Study Project Documentation: Review architectural, structural, and MEP drawings and specifications. Ensure all documents are current and reflect the latest design revisions.
- Break Down the Work Scope: Divide the project into logical sections or work categories, such as site preparation, foundations, superstructure, and finishes. Organise tasks systematically to ensure clarity and easy reference.
- Measure Quantities: Conduct detailed quantity take-offs based on the design drawings. Use standard units of measurement (e.g., cubic metres for concrete and square metres for tiling) as specified by the applicable BOQ standards.
- List Items with Descriptions: Provide clear and detailed descriptions for each item, specifying the type of material, quality, and scope of work. Avoid vague or incomplete descriptions to reduce the risk of misinterpretation.
- Apply Rates: Assign precise unit rates for materials, labour, and equipment based on current market data and the project location. Ensure the rates include allowances for overheads, profit margins, and contingencies.
- Organise the BOQ: Arrange the BOQ in a logical structure, grouping similar tasks under appropriate headings. Use a tabular format with columns for item descriptions, units, quantities, rates, and total costs for better clarity and usability.
- Cross-Check for Accuracy: Review measurements, calculations, and item entries to identify and correct errors or omissions. Collaborate with design teams, contractors, and consultants to resolve any discrepancies.
- Incorporate Provisional Items (If Needed): Include provisional sums for tasks or materials that are not yet fully defined. Clearly label these as provisional to distinguish them from finalised quantities.
- Follow BOQ Standards: Adhere to established standards such as NRM2 or CESMM4 to ensure consistency and alignment with industry practices. Ensure the BOQ complies with the project’s contractual requirements and meets stakeholder expectations.
To ensure accuracy and efficiency in BOQ preparation, you can use digital tools or software for quantity take-offs, as these can reduce manual errors. Additionally, it’s essential to regularly update the BOQ whenever design changes occur to reflect the most current information.
And don’t forget to include a margin for contingencies to account for any unexpected changes that may come up during the project. It’s also essential to take the time to understand the specific details in a Bill of Quantities (BOQ).
Who Prepares the Bill of Quantities?
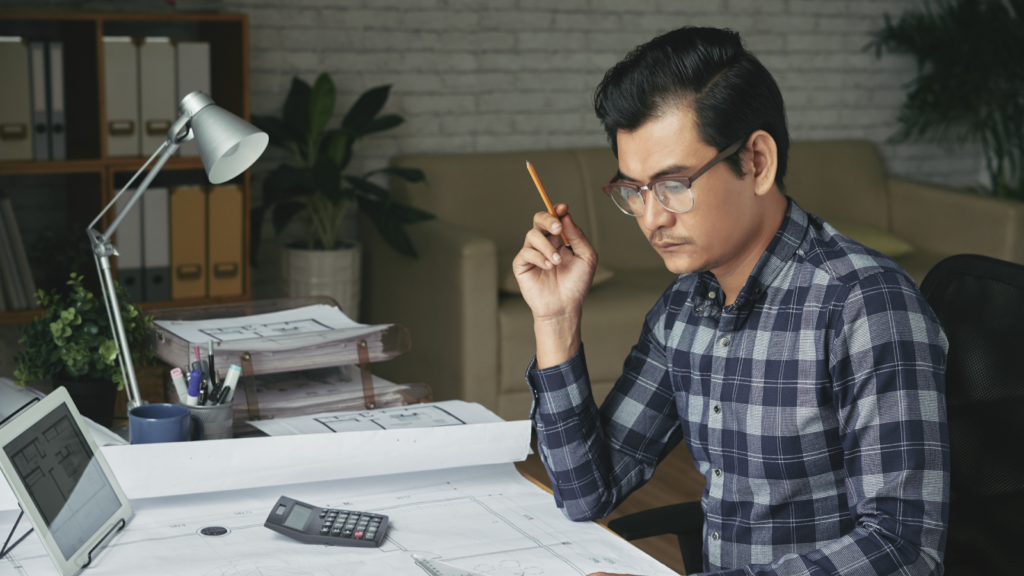
Preparing the Bill of Quantities (BOQ) is typically the responsibility of a Quantity Surveyor (QS) or a professional cost consultant. These experts specialise in measuring quantities, analysing project drawings, and creating detailed documentation to support construction projects. The Bill of Quantities is created by:
Quantity Surveyor (QS)
The Quantity Surveyor is responsible for preparing, reviewing, and finalising the BOQ based on design documents. The key tasks include:
- Analysing project drawings and specifications.
- Measuring and calculating quantities of materials and labour.
- Structuring the BOQ into clear and logical sections or categories.
- Applying standardised measurement methods, such as NRM2 or CESMM4.
- Ensuring accuracy and consistency in item descriptions, measurements, and costs.
Design Team (Architects/Engineers)
The design team provides detailed and accurate design drawings, specifications, and project scope to the Quantity Surveyor (QS). They collaborate with the QS to resolve vague or incomplete details to ensure clarity and accuracy in the BOQ.
Project Owner or Client
The project owner or client is responsible for approving the BOQ and providing guidance on project-specific requirements or budget constraints. They also review provisional sums or contingency allowances in the BOQ to ensure alignment with the project’s financial plans.
Consultants (If Applicable)
Consultants specialising in MEPF (mechanical, electrical, and plumbing, Fire) provide specific details for the BOQ. They also offer input on specialised work categories or provisional items to ensure that all aspects of the project are accurately represented.
While skilled professionals are responsible for creating a Bill of Quantities (BOQ), even the most experienced teams can encounter challenges.
Common Mistakes in BOQ & Ways to Resolve Them
Mistakes in the Bill of Quantities (BOQ) can happen even with thorough preparation. These errors result in cost overruns, disputes, or inefficiencies during a construction project. Addressing these issues is key to keeping things transparent, accurate, and running smoothly throughout the project.
The common mistakes in BOQ and their solutions are as follows:
Mistakes | Solutions |
Missing items or tasks lead to underestimations and budget discrepancies. | Cross-check the BOQ against detailed drawings and specifications.Conduct a thorough quantity takeoff and review. |
Errors in unit measurements or calculations cause inaccuracies in cost estimation. | Use standardised measurement methods like NRM2 or CESMM4.Double-check all calculations and quantities. |
Vague or unclear descriptions confuse contractors and stakeholders. | Use precise, detailed descriptions for materials, tasks, and specifications.Include references to relevant standards or specifications. |
Failure to account for uncertain or undefined items increases the risk of cost overruns. | Include provisional sums for tasks or materials with incomplete details.Clearly label these as provisional and update them as the project progresses. |
Incorrect or outdated rates lead to unrealistic cost estimations. | Research current market rates and factor in regional variations.Validate rates with industry benchmarks or contractor input. |
Listing the same item multiple times increases project costs and confuses. | Review the BOQ systematically to eliminate duplicate entries.Use BOQ preparation software to identify redundancies. |
Failing to allocate a contingency budget increases project risk. | Include a reasonable contingency allowance based on project complexity and risks. |
Poor organisation makes the BOQ challenging to understand and use effectively. | Follow a logical structure, grouping items by work categories or project phases.Use consistent formatting and headings for clarity. |
Failing to revise the BOQ after design changes leads to outdated quantities and costs. | Regularly update the BOQ to reflect design revisions. |
Missing costs for overheads, wastage, or site-specific requirements cause budget shortfalls. | Include allowances for overheads, material wastage, and site conditions in the BOQ. |
By addressing these common mistakes early on, you can improve the accuracy & reliability of the Bill of Quantities (BOQ), helping to make the construction process smoother and leading to better project outcomes. BIM Supports GREEN EARTH.
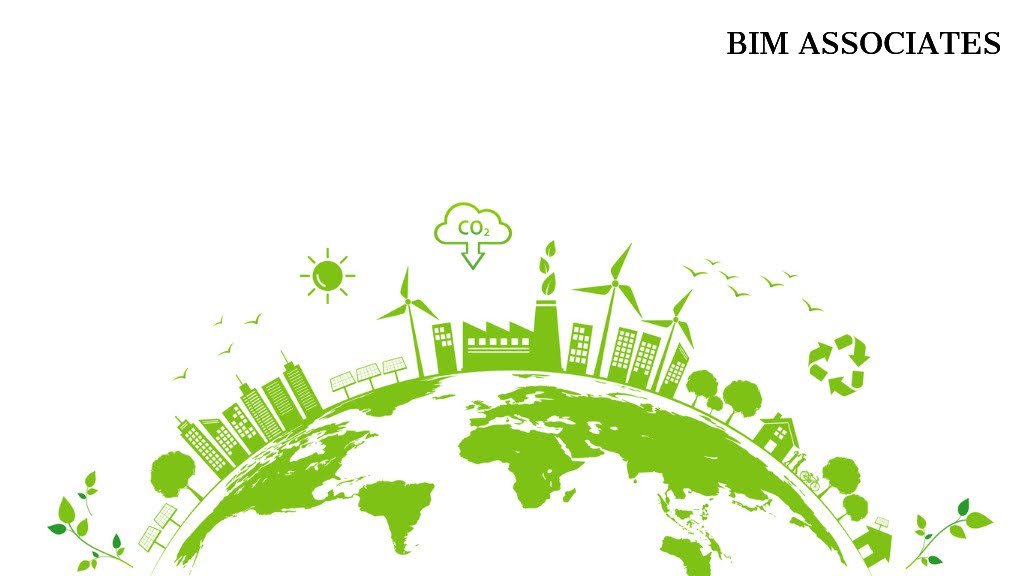
Conclusion
Understanding the Bill of Quantities (BOQ) is key for anyone involved in construction projects. It offers a detailed breakdown of materials, labour, and costs, making it an essential tool for accurate budgeting, clear tendering, and efficient project management.
BOQ does more than just estimate costs — it encourages stakeholder collaboration, helps reduce disputes, and ensures that every part of the project is accounted for correctly. A well-prepared BOQ also helps simplify project planning and execution by making resource allocation easier, enabling better progress tracking, and reducing the risk of cost overruns.
Are you looking for BIM Solutions?
BIM ASSOCIATES is your one-stop BIM Solution provider for the Architecture and Structure discipline. Their solutions help clients with better decision-making, cost-saving, efficient construction planning, and green earth initiatives.
You might also like: BIM Levels and Stages of Development Explained.
FAQs (Frequently Asked Questions)
1. How do you calculate BOQ?
To calculate BOQ, follow these steps:
- Prepare a spreadsheet to organise all data.
- Break down the work into clear sections or categories.
- Estimate the labour required for each task.
- Make an initial cost estimate based on the quantities and rates.
- Draft a project schedule to align with the estimated costs.
- Continue using the BOQ throughout the project to track progress and manage costs.
2. What is the difference between BOQ and BOM in construction?
A Bill of Quantities (BOQ) includes all project costs, covering materials, labour, and other expenses. In contrast, a Bill of Materials (BOM) focuses solely on the materials needed for the project. General contractors may include a BOM in the bid packages for subcontractors, regardless of the project’s size.
3. What is the purpose of BOQ?
The primary purpose of the BOQ is to ensure fairness, transparency, and clarity in the bidding process. It helps suppliers and contractors understand the project’s specifications, quantities, and requirements, enabling them to submit competitive and accurate proposals.