- Understanding Digital Twins and BIM
- What is a Digital Twin?
- What is Building Information Modelling (BIM)?
- What’s the Difference between BIM, Revit, and Digital Twin?
- What are the Capabilities of Digital Twins?
- Real-Time Monitoring & Data Integration
- Predictive Maintenance & Problem Detection
- Simulation & Testing
- Improving Efficiency & Operations
- Remote Monitoring & Control
- Lifecycle Management & Sustainability
- Six Key Data Considerations for Value-Adding Digital Twins
- Extending the Value of BIM with a Digital Twin
- Real-Time Data for Better Insights
- Smarter Decision-Making
- Improving Efficiency and Reducing Costs
- Better Collaboration Across Teams
- Improving Sustainability
- What are the 5 Stages of Digital Twin?
- Challenges & Solutions While Implementing Digital Twin
- Latest Trends in Using Digital Twins in Construction
- Conclusion
- FAQs (Frequently Asked Questions)
Building Information Modelling (BIM) has helped construction teams create detailed 3D models that improve planning and collaboration. However, these models mainly focus on the design and construction phases.
Digital Twin technology takes BIM a step further by adding real-time data and live simulations. This allows teams to monitor, analyse, and improve buildings even after construction is complete, making it a valuable tool for long-term management.
As more industries recognise the benefits of Digital Twins, their adoption is growing. The global market for this technology is expected to reach $73.5 billion by 2027, showing its increasing role in improving efficiency and reducing costs.
By combining BIM with Digital Twins, construction teams can lower maintenance costs, optimise performance, and make smarter decisions throughout a building’s lifecycle.
In this article, you’ll explore the key features of BIM and Digital Twins, how they are different, and how they work together to improve project management. In addition, you’ll also learn important data factors, challenges in using these technologies, and the latest trends shaping the future of construction.
Understanding Digital Twins and BIM
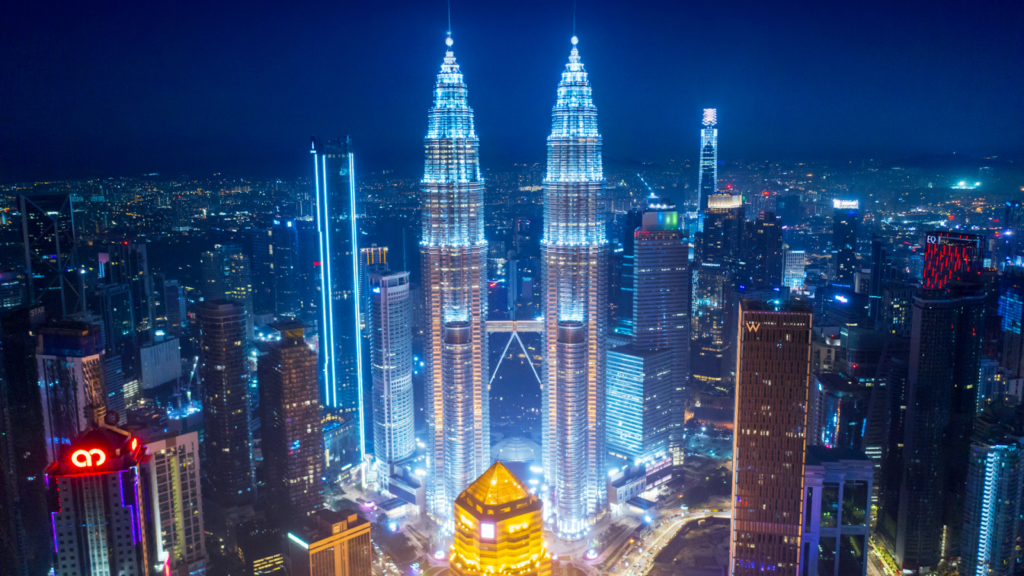
Digital technology is reshaping the modern construction industry, redefining the planning, construction, and upkeep of buildings and infrastructure. Among the most impactful innovations are Digital Twins and Building Information Modelling (BIM), which are changing the way projects are designed, monitored, and maintained.
What is a Digital Twin?
A Digital Twin is a digital replica of a real project, object, process, or system that updates in real time. Unlike regular 3D models, which stay the same, a Digital Twin changes as the real thing changes. It does this by using data from smart sensors, artificial intelligence, and analytics.
This live connection helps businesses track performance, predict problems, and improve efficiency using real data. In construction and infrastructure, Digital Twins helps manage assets, save energy, and cut maintenance costs. They also allow teams to test different scenarios, find issues, and make better decisions before making changes in the real world.
What is Building Information Modelling (BIM)?
Building Information Modelling (BIM) is a digital method used in architecture, engineering, and construction to create and manage detailed 3D models of buildings and infrastructure. Unlike traditional blueprints, BIM combines 3D designs with important details like materials, costs, schedules, and maintenance plans.
This helps architects, engineers, and contractors collaborate smoothly, spot design problems early, and improve project efficiency. BIM makes it easier to visualise designs, organise tasks, and make better decisions throughout a building’s life—from planning and construction to long-term upkeep.
While BIM improves project efficiency through data-driven decision-making, many often wonder how it compares to other technologies like Revit and Digital Twin.
What’s the Difference between BIM, Revit, and Digital Twin?
BIM is a process for creating and managing digital models of buildings, while Revit is a software that helps professionals build these BIM models. Digital Twins, on the other hand, are real-time virtual copies of physical assets that continuously update as changes occur.
Although these tools are often mentioned together, they serve different purposes. Understanding their differences helps professionals simplify their work and make better, data-driven decisions.
Below are the key differences between BIM, Revit, and Digital Twin:
Feature | BIM (Building Information Modelling) | Revit | Digital Twin |
Definition | A process for creating and managing 3D models with data throughout a building’s lifecycle. | A software developed by Autodesk for BIM modelling and documentation. | A live digital copy of a physical asset, system, or process that updates effectively. |
Purpose | Improves collaboration, design accuracy, and project efficiency. | Used to create detailed BIM models for architecture, engineering, and construction. | Enables real-time monitoring, predictive analytics, and remote asset management. |
Data Integration | Includes static design, material specifications, costs, and schedules. | Focuses on 3D modelling, documentation, and parametric design. | Integrates IoT, AI, real-time sensor data, and predictive analytics. |
Interactivity | Primarily used during design and construction phases. | Allows design modifications and documentation updates. | Continuously updates and evolves throughout the asset’s lifecycle. |
Use Case | Used for planning, designing, constructing, and maintaining buildings and infrastructure. | Architects, engineers, and construction professionals utilise it to create BIM models. | Used in smart cities, manufacturing, construction monitoring, and infrastructure management. |
Lifecycle Focus | Covers design, construction, and limited post-construction phases. | Primarily focused on design and documentation. | Covers the entire lifecycle, including operations, maintenance, and real-time performance tracking. |
Visualisation | Provides detailed 3D models for design and planning. | Generates parametric 3D models with accurate measurements and documentation. | Offers a live, real-time virtual representation of physical assets. |
Predictive Analytics | Limited to static analysis and design simulations. | Includes structural analysis and performance evaluation tools. | Uses AI and IoT for predictive maintenance and operational efficiency. |
Industry Application | Construction, infrastructure, facility management. | Architecture, engineering, and construction (AEC). | Smart buildings, urban planning, healthcare, manufacturing, energy, and industrial IoT. |
Understanding how BIM, Revit, and Digital Twin differ provides clarity on their unique roles in construction and design. It helps see how Digital Twin improves real-time monitoring, analysis, and decision-making in construction projects.
Also read: A Guide to Building Information Modelling (BIM) Impact on Modern Construction Industry.
What are the Capabilities of Digital Twins?
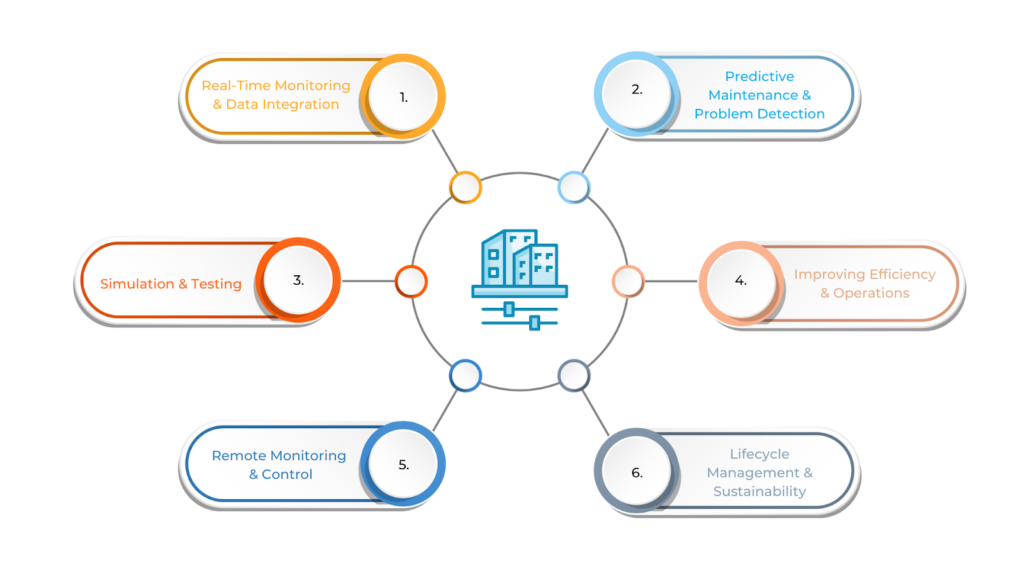
Digital twins are changing industries by creating virtual copies of real things like buildings, machines, and processes. These smart models use live data, advanced simulations, and predictions to help businesses make better decisions, improve performance, and avoid problems.
Industries like construction, manufacturing, healthcare, and smart cities use digital twins to track operations, test different ideas, and work more efficiently than ever.
Digital Twins help businesses make better decisions, improve efficiency, and predict problems before they happen. Below are some of its key features:
Real-Time Monitoring & Data Integration
Digital Twins collect and analyse data from smart sensors, cloud systems, and AI to create a live digital version of real assets. This allows businesses to track equipment performance, building conditions, and environmental factors in real-time.
Predictive Maintenance & Problem Detection
Using past data and AI, Digital Twins can predict when equipment might fail. This helps businesses fix issues before they become serious, reducing downtime and extending the life of assets.
Simulation & Testing
Engineers and managers can use Digital Twins to test different scenarios, such as how much weight a structure can handle, energy usage, or system performance. This helps them make improvements before making physical changes.
Improving Efficiency & Operations
Industries like construction, manufacturing, and healthcare use Digital Twins to simplify processes, reduce delays, and make better use of resources, saving time and money.
Remote Monitoring & Control
Since Digital Twins work in real time, businesses can track and control assets from anywhere. This is especially useful for managing large projects, smart cities, and industrial sites without requiring to be on-site.
Lifecycle Management & Sustainability
Digital Twins provide a complete view of an asset from design to construction, maintenance, and even retirement. This helps businesses use resources wisely, reduce waste, and follow environmental regulations.
By combining AI, smart sensors, and advanced data analysis, Digital Twins helps businesses improve performance, lower risks, and bring innovation.
Ready to simplify your BIM projects and achieve these benefits?
BIM ASSOCIATES is your one-stop BIM Solution provider for Revit Architectural and Structural Solutions. They coordinate with your team to develop, record, and streamline the BIM Revit Model, along with the sheets, Bill of Quantities, Bill of Materials, and clash coordination.
To get the most out of Digital Twins, it’s essential to manage data well. Attention to key data factors ensures these models provide accurate insights for better decision-making.
Six Key Data Considerations for Value-Adding Digital Twins
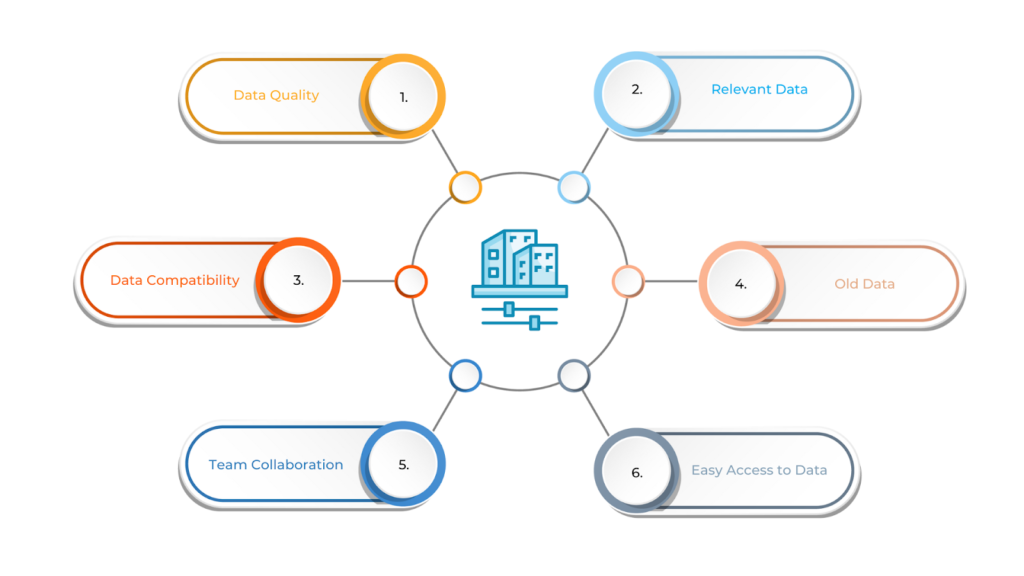
Digital Twins are changing industries by offering real-time data, predictions, and advanced simulations. However, organisations need a clear plan to make Digital Twins truly useful. This includes setting specific goals, using the right BIM processes, and effectively connecting live data.
Before creating BIM models and linking them with real-time information, six important factors must be considered to ensure the Digital Twin is strong and effective. Below are those six data factors:
- Data Quality: Your insights are only as good as the data you use. It’s important to keep static and real-time data accurate and reliable while keeping costs in check.
- Relevant Data: Not all design data is helpful for operations. You must decide which data sources are necessary at the design and operational stages.
- Data Compatibility: Different technologies use different data formats. To ensure smooth data sharing, you must carefully plan how different systems will work together.
- Old Data: New projects can start fresh with a digital-first approach, but older buildings and systems may lack helpful data. Upgrading and organising existing data can bring big benefits.
- Team Collaboration: Departments working in isolation can slow things down. Encouraging teamwork and open communication across different teams will lead to better results throughout the project.
- Easy Access to Data: Digital Twin information should be easy for end users to access without requiring them to learn complex IT systems.
To get the most from Digital Twins, it’s important to collect, manage, and use data properly. Combining Digital Twins with BIM can improve project insights, management, and efficiency.
Extending the Value of BIM with a Digital Twin
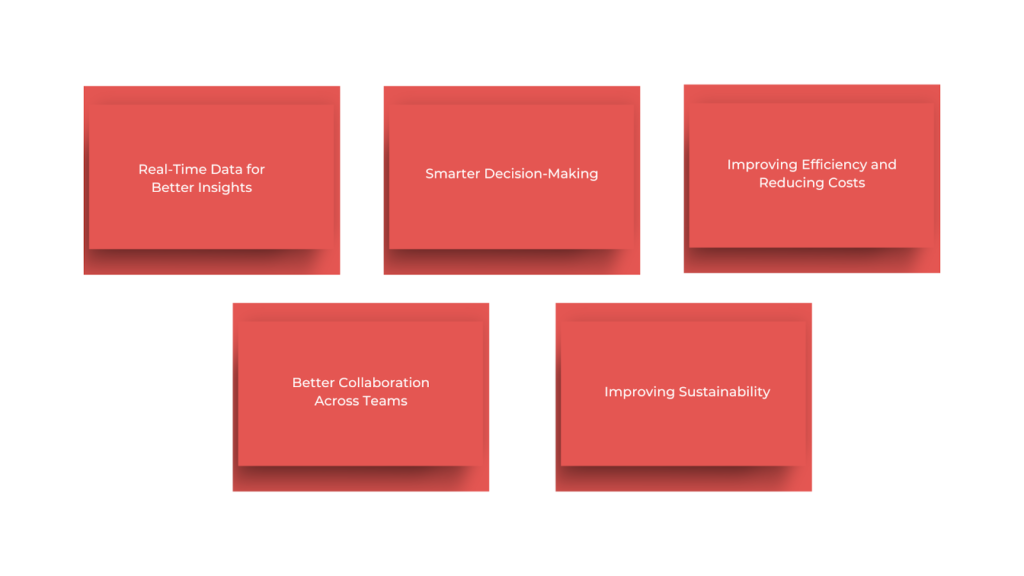
Building Information Modelling (BIM) has been a valuable tool in architecture, engineering, and construction (AEC), helping teams design, plan, and manage projects digitally. However, BIM models are static, which means they represent a project at a specific stage, usually during design and construction.
Digital Twins takes BIM further by adding real-time data and creating a virtual version that evolves with the physical asset. By combining BIM with Digital Twins, organisations can extend the use of their models beyond construction.
Some key benefits of this integration include:
Real-Time Data for Better Insights
While BIM captures design and construction details, a Digital Twin adds real-time data from sensors, IoT devices, and other sources. This allows the model to reflect actual performance, environmental conditions, and wear and tear, making it a “living” version of the asset.
Smarter Decision-Making
With real-time insights, teams can monitor performance, predict maintenance needs, and optimise resource use. Whether adjusting HVAC systems, reducing energy consumption, or preventing equipment failures, the combination of BIM and Digital Twins supports smarter, data-driven decisions.
Improving Efficiency and Reducing Costs
BIM helps with project planning, but Digital Twins improve post-construction efficiency. Facilities managers can track real-time conditions, schedule maintenance before problems occur, and extend the life of assets, reducing costly repairs and downtime.
Better Collaboration Across Teams
Digital Twins and BIM provide a shared platform for architects, engineers, contractors, and facility managers. Real-time data keeps everyone updated, improves communication, and ensures that decisions are based on current conditions.
Improving Sustainability
Using Digital Twins alongside BIM helps teams manage energy use, reduce waste, and meet sustainability goals. With access to real-time performance data, organisations can improve efficiency and adapt to new, greener technologies.
BIM lays the foundation for construction, while Digital Twins brings it to life with live data and intelligent operations. Together, they create a complete, long-term solution that improves performance, lowers costs, and ensures sustainability after construction. To get the most out of Digital Twins, it’s crucial to understand how they develop.
What are the 5 Stages of Digital Twin?
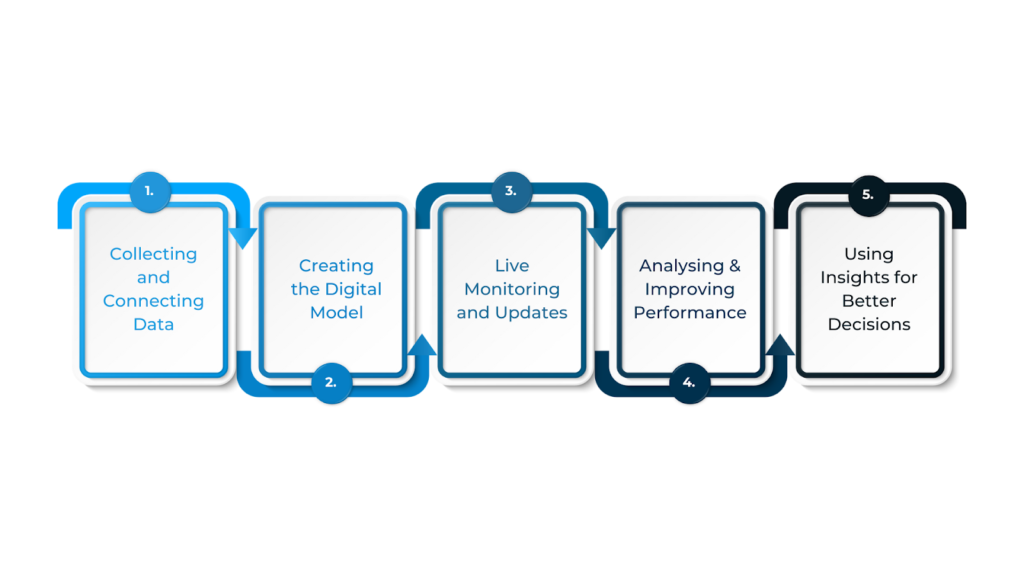
Digital Twins grow in stages, with each step adding more data, better simulations, and smarter features. Each phase improves efficiency, predicts issues, and enables real-time improvements. Understanding these stages helps organisations make the most of Digital Twins.
Creating a Digital Twin is a step-by-step process, where each stage builds on the previous one to develop a fully functional and valuable model. Below are the five main stages of Digital Twin development:
- Collecting and Connecting Data
The first step is gathering data from real-world objects using sensors, IoT devices, and other sources. This data helps create a digital version of the physical asset. It’s essential to ensure the data is accurate and updated regularly to build a reliable Digital Twin.
- Creating the Digital Model
Next, a virtual version of the real-world object is created. This model includes details like shape, size, and how it functions. Some parts of the model stay the same (like structure), while others change over time (like performance). This step ensures the Digital Twin accurately represents the real asset.
- Live Monitoring and Updates
At this stage, the Digital Twin becomes “live” by continuously receiving real-time data from sensors and connected devices. This keeps the model updated, allowing teams to monitor conditions, track changes, and make informed decisions.
- Analysing and Improving Performance
Now, advanced tools like AI and data analytics are used to find problems, improve efficiency, and predict potential failures. These insights prevent breakdowns, reduce costs, and optimise operations.
- Using Insights for Better Decisions
The final step is applying what’s learned from the Digital Twin to make better decisions in the real world. This could mean adjusting maintenance schedules, improving designs, or making operations more efficient.
These five stages work together to create a powerful tool for tracking, improving, and managing physical assets over time. While Digital Twins offer significant benefits, implementing them comes with challenges.
Challenges & Solutions While Implementing Digital Twin
Digital Twins can improve efficiency, predict maintenance needs, and support better decision-making across many industries. However, like any new technology, they come with challenges. Understanding these challenges is important to get the most value out of Digital Twins.
Below are the challenges and their effective solutions while implementing digital twin:
Challenges | Solutions |
Data Integration Issues | Set up reliable data collection systems and ensure compatibility with existing infrastructure using standardised data formats and APIs for smooth integration. |
High Initial Investment | Start with a small project to show the benefits, then expand step by step while finding ways to manage costs. |
Real-time Data Synchronisation | Use IoT devices, cloud, and edge computing to keep data updated in real-time and ensure a strong network for smooth data flow. |
Data Security and Privacy Concerns | Use strong cybersecurity measures like encryption, access control, and secure cloud storage to protect data and conduct regular security checks. |
Lack of Skilled Personnel | Train employees and work with experts to build a team skilled in data analytics, IoT, and Digital Twin technology. |
Complexity of Modelling Physical Assets | Start with small, simple models before expanding, and use automated tools to make modelling easier and more accurate. |
Maintenance and Upkeep of the Digital Twin | Create a team to manage and update the Digital Twin, using automation to keep data accurate and up-to-date. |
Resistance to Change | Teach stakeholders the benefits of Digital Twins with real examples and pilot projects, and encourage a culture of innovation. |
Lack of Standardisation | Work with industry groups to create universal standards for Digital Twins, ensuring they work smoothly across different systems. |
As industries find solutions to challenges, Digital Twins keep improving and creating new opportunities in construction. New trends are changing how these virtual models help make projects more efficient and smarter for better decision-making.
Latest Trends in Using Digital Twins in Construction
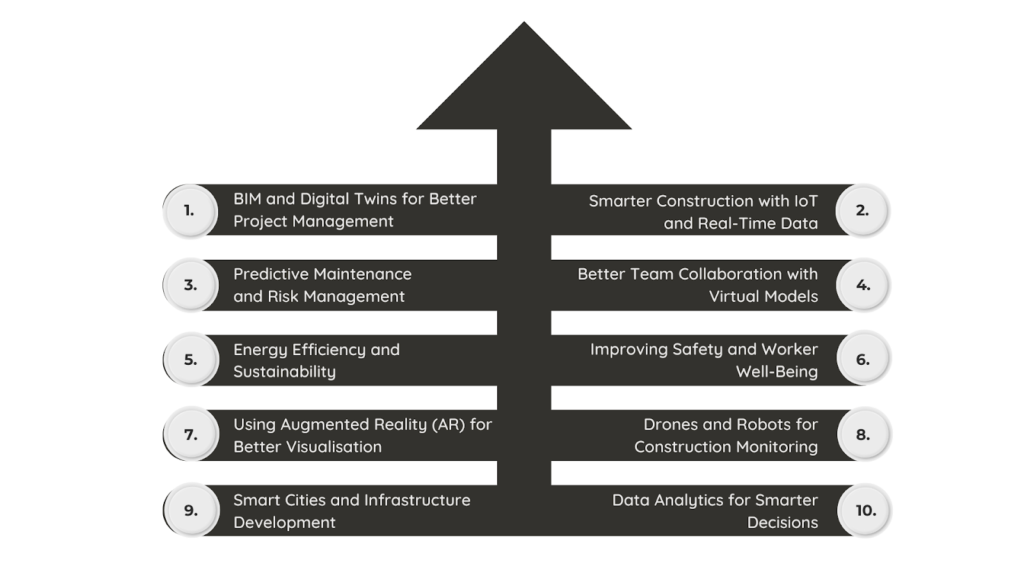
Construction teams are adopting Digital Twins to seek smarter and more efficient work methods. These virtual models of real buildings provide real-time data and help teams simplify workflows, improve safety, and build in a more sustainable way.
Some key trends driving this technology include its integration with Building Information Modelling (BIM) and the use of AI and IoT for predictive maintenance. Below are some of the latest ways by which Digital Twins are changing the construction industry:
- BIM and Digital Twins for Better Project Management
Building Information Modelling (BIM) and Digital Twins improve construction projects. BIM helps with design and planning, while Digital Twins provides live updates and tracking once construction starts. This combination helps teams make better decisions, monitor performance, and solve issues early—even after the project is finished.
- Smarter Construction with IoT and Real-Time Data
Digital Twins work with IoT devices to create smarter construction sites. Sensors on equipment, materials, and buildings collect data on temperature, stress levels, and other conditions. This live data helps managers improve safety, avoid delays, and prevent damage.
- Predictive Maintenance and Risk Management
Digital Twins help in predictions when construction equipment and structures might fail. By analysing data, they alert teams before problems occur, reducing downtime, improving safety, and extending equipment life. They also spot risks in construction projects before they turn into costly issues.
- Better Team Collaboration with Virtual Models
Digital Twins creates a shared virtual version of a construction site that updates in real time. This allows architects, engineers, contractors, and facility managers to work with the same data, reducing mistakes and improving communication.
- Energy Efficiency and Sustainability
Digital Twins help design and manage energy-efficient buildings. They simulate energy use, heating, and cooling, allowing teams to optimise systems and reduce waste. They also track the environmental impact of construction and help companies meet sustainability goals.
- Improving Safety and Worker Well-Being
Digital Twins help improve construction site safety by simulating hazards and monitoring safety in real time. Wearable devices and sensors can track workers’ health and location, reducing risks on large or high-risk sites.
- Using Augmented Reality (AR) for Better Visualisation
When combined with Digital Twins, Augmented Reality (AR) allows workers to see digital models over real-world construction sites. This helps them understand designs better, spot potential issues, and make quick, informed decisions.
- Drones and Robots for Construction Monitoring
Drones capture aerial images of construction sites, while robots can survey areas, move materials, or assist with assembly. These technologies collect data for Digital Twins, improving efficiency, reducing costs, and increasing accuracy.
- Smart Cities and Infrastructure Development
Digital Twins are being utilised to create virtual models of entire cities. City planners and authorities use them to monitor traffic, energy use, and waste management in real time. They also help plan and integrate new construction projects with existing infrastructure.
- Data Analytics for Smarter Decisions
Digital Twins generate large amounts of data, which AI and machine learning can analyse to find patterns and predict trends. This helps construction managers make data-driven decisions, use resources wisely, and improve project efficiency.
BIM Supports GREEN EARTH.
Conclusion
Digital Twins and Building Information Modelling (BIM) are changing the construction industry by working together to improve projects. When used together, these technologies help construction teams reduce risks and enhance collaboration at every project stage.
By combining BIM and Digital Twins, businesses can simplify workflows, make real-time adjustments, and even predict future issues. Companies that embrace both technologies can build smarter, work more efficiently, and stay ahead in the industry.
Are you looking for BIM solutions?
BIM ASSOCIATES is your one-stop BIM Solution provider for the Architecture and Structure discipline. Their solutions help clients with better decision-making, cost-saving, efficient construction planning, and green earth initiatives.
You might also like: BIM Levels and Stages of Development Explained.
FAQs (Frequently Asked Questions)
1. Is digital twin a 3D model?
A Digital Twin is not only a 3D model; it’s a live virtual copy that uses real-time data to track and analyse a physical object or system.
2. What are the 4 key types of Digital Twins?
There are 4 main types of digital twins:
- Component Twin: A digital version of a single part.
- Product Twin: A digital model of an entire product.
- System Twin: A replica of multiple connected products.
- Process Twin: A digital version of a full process or workflow.
3. Do Digital Twins use AI?
Digital twins create virtual copies of real things, while AI helps analyse data, make predictions, and automate tasks. AI can be used with digital twins to improve decision-making.