The construction industry is experiencing an increase in the implementation of digital technologies such as BIM. Among these innovations, concrete modular formwork stands out as one of the most impactful, driving efficiency, sustainability, and precision in concrete construction.
Integrating modular formwork and BIM offers a data-driven approach that optimizes the entire construction lifecycle. This alliance is gaining traction in the UK, a global leader in standards and innovation, where BIM-driven modular formwork systems are being rapidly adopted.
In this article, you’ll gain insights into the connection between BIM and concrete modular formwork. In addition, you will discover the key elements of modular formwork, its implementation through BIM, software tools to use, and the UK regulatory framework. Let’s start!
Introduction to Concrete Modular Formwork Using BIM
Concrete modular formwork is a major innovation in modern construction, offering a more organised and reusable approach to building concrete structures. It uses pre-made, interchangeable parts, streamlining the process for greater speed and efficiency.
The key benefits include quicker assembly and disassembly, reduced construction time, and uniform, factory-manufactured components that minimize errors during installation. Additionally, its reusable nature helps lower material waste and significantly reduce costs.
This modular formwork is becoming increasingly popular across different construction projects due to its flexibility in handling different project sizes and complexities. Among these, Building Information Modeling (BIM) stands out as a transformative tool that complements and enhances concrete modular formwork.
Site Picture of Modular Formwork
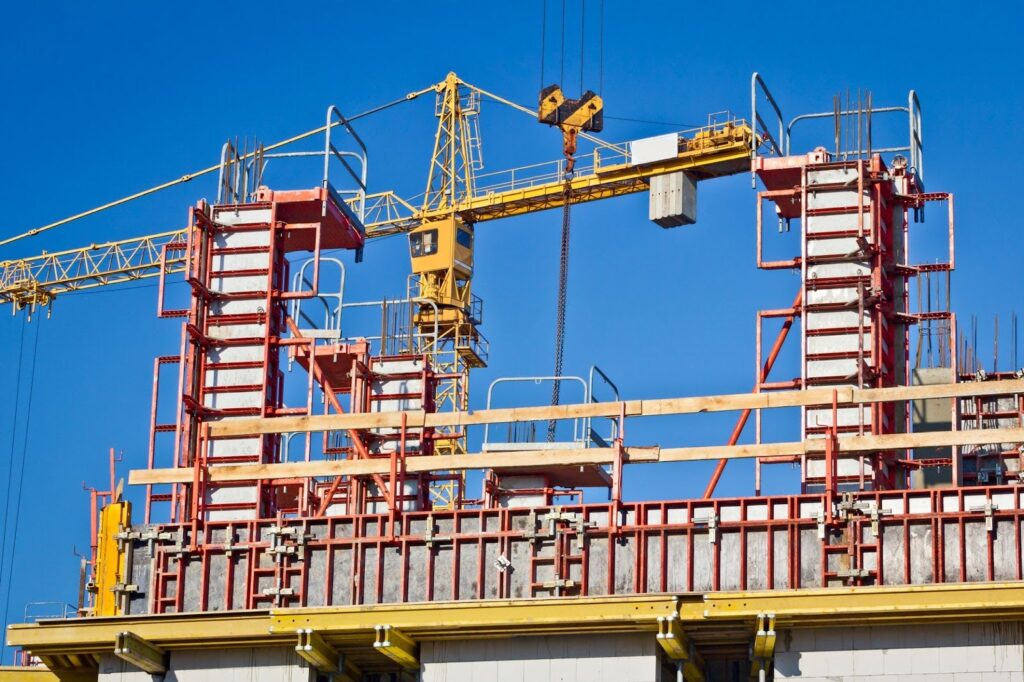
This image shows the on-site use of modular formwork, highlighting its precision-engineered components and efficient assembly process. The neatly arranged panels emphasize the system’s flexibility to meet different structural needs, ensuring consistent quality and fast construction. This visual effectively showcases its importance in modern construction, blending innovation with practicality.
How Modular Formwork Differs from Conventional Formwork?
Formwork is vital in concrete construction, serving as a temporary mold for freshly poured concrete until it hardens. Advancements in construction technology have introduced modular formwork systems, offering significant improvements over traditional methods.
Conventional formwork often uses site-assembled materials like timber, plywood, and steel. In contrast, modular formwork consists of pre-engineered, reusable components designed for greater efficiency and precision. When combined with modern tools like Building Information Modeling (BIM), modular formwork is transforming construction processes, particularly in the UK.
Let us take a closer look at the key differences between modular formwork and conventional formwork.
Aspect | Modular Formwork | Conventional Formwork |
Design and Configuration | Pre-engineered, reusable, and modular components designed to meet specific project requirements. | Built on-site using traditional materials like wood, plywood, or steel, tailored for each project. |
Construction Time | Faster assembly and disassembly due to prefabricated components. | Slower due to on-site customization and manual assembly. |
Material Efficiency | High efficiency; minimal waste as components are reusable and standardized. | Low efficiency; often results in material waste due to on-site modifications. |
Durability | High durability, made from durable materials such as aluminum, steel, or composites. | Variable durability depends on material quality and is often prone to wear and tear. |
Cost Efficiency | Higher initial investment but cost-effective for large or repeated projects. | Lower initial cost but higher long-term expenses due to limited reusability. |
Precision | High; factory-made components ensure accuracy and consistent quality. | Lower; manual construction increases the risk of human error. |
Safety | Superior safety features, including locking mechanisms and load capacities, are designed for compliance. | Relies on on-site practices, often less robust than modular systems. |
Environmental Impact | Lower environmental impact due to reusable materials and reduced waste. | Higher environmental impact due to significant waste and limited reusability. |
Integration with BIM | Highly compatible; BIM effectively models, optimizes and manages modular systems. | Limited compatibility; requires more manual modeling and integration into BIM workflows. |
Relationship Between BIM and Modular Formwork for Concrete
Building Information Modelling (BIM) and concrete modular formwork work well together to improve modern construction efficiency, precision, and sustainability. BIM is a useful tool for planning, designing, and managing modular formwork systems, while modular formwork benefits from BIM’s ability to improve workflows and reduce mistakes.
If you want to understand the relationship between BIM and concrete modular formwork, look at these pointers:
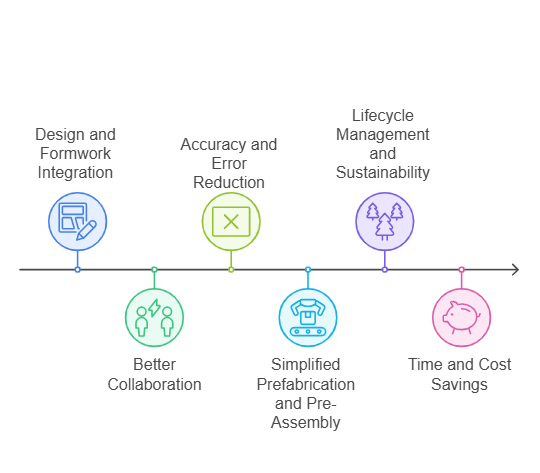
- Design and Formwork Integration: BIM offers a digital platform to design modular formwork accurately, allowing designers to integrate formwork components into the overall structure. Designers can use a 3D model to check if all parts fit together correctly by ensuring smooth coordination with architectural and structural needs.
- Better Collaboration: BIM helps team members work together in real time through a shared data system. It has fostered enhanced collaboration and refocused the team on the project’s goals, resulting in improved outcomes.
- Accuracy and Error Reduction: BIM’s clash detection helps identify problems between the formwork and other elements, such as reinforcement or mechanical systems, early on. The detailed simulations ensure the formwork is strong enough to handle concrete pressure.
- Simplified Prefabrication and Pre-Assembly: BIM creates detailed drawings and instructions for modular formwork components, making the prefabrication and pre-assembly process more efficient. The digital model also helps plan logistics, such as transportation and assembly on-site.
- Lifecycle Management and Sustainability: BIM acts as a digital twin of the formwork system by keeping track of its design, use, and eventual removal. It also helps assess the environmental impact of concrete structures by supporting green construction goals.
- Time and Cost Savings: BIM with modular formwork reduces project timelines by improving assembly sequences and material efficiency. It also provides accurate cost estimates and material needs by controlling budgets and minimising waste.
As BIM enhances the efficiency and precision of modular formwork, its integration into construction practices extends to the specific elements required for projects. In the UK, understanding these key elements is essential for ensuring seamless implementation and optimal performance on-site.
Additionally, BIM enables seamless coordination with other trades, ensures compliance with UK construction standards, and improves project timelines by reducing rework. Adopting BIM in modular formwork systems offers a strategic approach to boosting productivity, reducing costs, and enhancing sustainability in UK construction projects.
Key Components of Modular Formwork for Concrete in the UK
Modular formwork systems are made up of ready-to-use, reusable parts designed to shape concrete into specific structures. These highly standardized components make them flexible, efficient, and reusable across various projects.
The main components of modular formwork for concrete include:

Aspect | Components |
Panels | Flat or curved parts that touch the concrete, shaping its surface. Come in different sizes to fit various project needs. |
Frames | Strong supports that keep the panels rigid and hold up against the pressure of wet concrete. |
Connectors and Fasteners | Tools like clamps, pins, and wedges securely hold the panels and frames together, making the assembly easy and stable during pouring. |
Ties and Spacers | Items used to keep walls and slabs at the right thickness and resist the outward pressure of concrete. |
Supports and Props | Adjustable vertical supports that keep the formwork in the right position and properly aligned. |
Corner and Edge Components | Special pieces build corners, edges, and junctions in walls and columns, helping formwork panels fit together smoothly. |
These modular parts can be arranged in different configurations to accommodate various building designs and construction needs, making them highly versatile for multiple projects.
While the configuration and flexibility of modular parts are essential for diverse construction needs, the choice of materials plays a pivotal role in determining the durability and efficiency of the formwork system.
Common Materials Used in Modular Formwork
Modular formwork systems use strong, lightweight, and reusable materials to make construction efficient and cost-effective. Here are those common materials:

Materials | Why it’s used |
Aluminium | Lightweight and rust-resistant, making it easy to handle and great for projects needing frequent reuse. The aluminum formwork system saves time by avoiding many on-site tasks. |
Steel | Known for its strength & durability, steel is ideal for large or heavy projects like bridges and tall buildings. |
Plastic/Composite Materials | Light and affordable, plastic formwork works well for repetitive designs, offering smooth finishes and resistance to weather and chemicals. |
Plywood with Metal Frames | Combines flexible plywood with sturdy metal frames, making it a budget-friendly choice for smaller or medium projects. |
The material you choose depends on the project size, design complexity, and durability of the formwork. Choosing the right material is one part of the equation; the design and configuration of modular formwork systems must also align with the project’s specific requirements.
Design and Configuration Considerations for Modular Formwork Systems
The success of a modular formwork system depends on how well it is designed and configured to meet the project’s needs. A well-designed system addresses the project’s specific needs, such as the structure’s dimensions, the type and amount of concrete, and the construction timeline.
Customizing the formwork design to these factors optimizes material usage, lowers costs, and improves overall efficiency.
Here are the essential factors to consider for design and configurations:
- Strength: The formwork system must be strong enough to handle the weight of wet concrete during pouring and curing. It should support loads of approximately 2,400 kg/m³, with a total design load of 6.0–8.0 kN/m² for typical applications.
- Flexibility: Modular formwork should be able to fit different shapes, sizes, and types of concrete structures. It should be easy to adjust for different project stages, making it flexible for various designs.
- Easy to Put Together: Components should connect quickly and accurately, using lightweight materials and user-friendly designs to enhance efficiency and safety during installation.
- Smooth Surface: High-quality, non-porous materials ensure a smooth concrete finish, minimising defects and reducing the need for additional post-construction work.
- Transport and Storage: Components should be easy to stack and transport, with protective coatings to enhance durability and reduce maintenance needs.
- Long Life: A building built using steel modular formwork is given a usable life of 100+ years.
- Environmentally Friendly: The system should be reusable and recyclable to reduce environmental impact. Designers should choose materials and methods that follow green building standards to make the system more sustainable. BIM Supports GREEN EARTH.
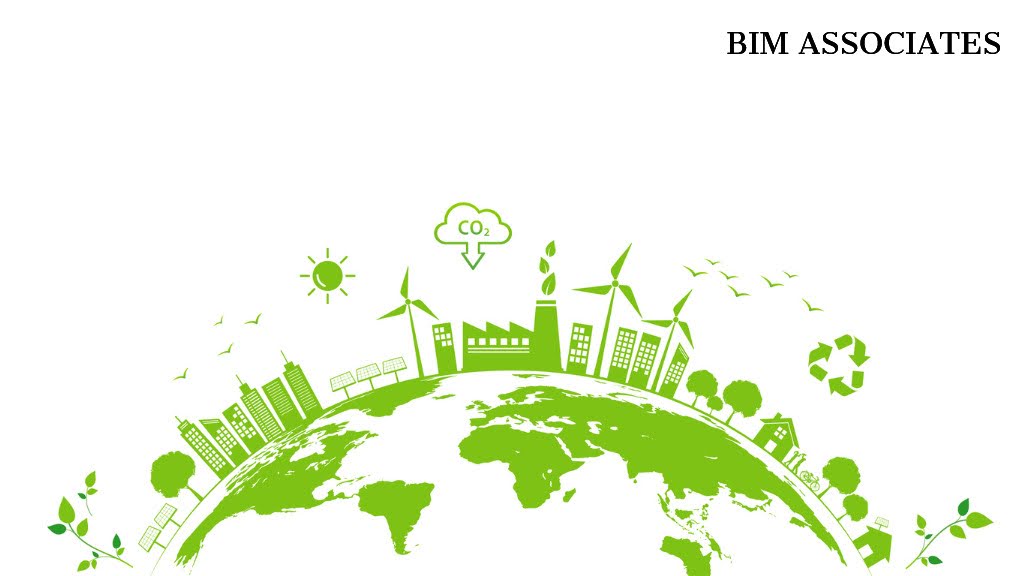
By focusing on these factors, modular formwork systems can improve efficiency, cut costs, and meet the unique demands of various construction projects.
With these design and configuration considerations in mind, the next step is understanding how to implement modular formwork systems effectively, especially when integrating BIM.
Implementation Process of Modular Formwork Using BIM in the UK
Implementing BIM in modular formwork follows a structured and collaborative approach, ensuring accuracy, efficiency, and successful outcomes. BIM integration enables detailed modeling of formwork systems, which helps with precise planning, reduces material waste, and optimizes costs. It also supports real-time visualization and clash detection, reducing errors and speeding up project timelines.
Here’s the step-by-step process for implementing Modular Formwork using BIM:
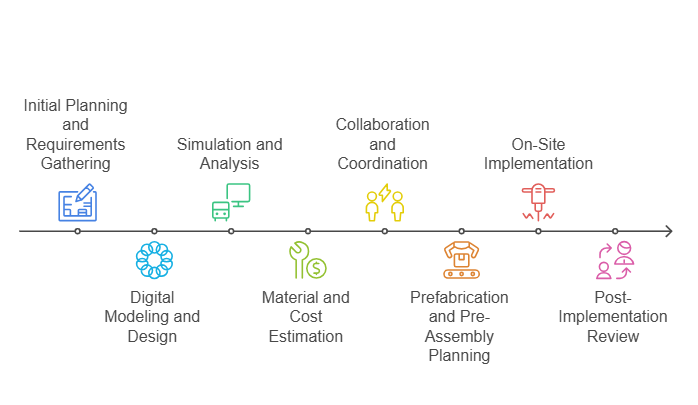
Step 1: Initial Planning and Requirements Gathering
This stage defines the project’s objectives, scope, and expected outcomes to create an execution plan. The specific needs for modular formwork, such as size, materials, and design, are identified to fit the project.
Also, essential performance indicators (KPIs) are set to measure how well BIM is helping to achieve the project’s goals, like accuracy, efficiency, and sustainability.
Step 2: Digital Modelling and Design
A detailed 3D model of the project is created using advanced BIM tools, encompassing all design elements, including structure, architecture, and mechanical systems. This ensures seamless integration and compatibility.
The modular formwork is then designed and added to the model to meet project standards. Clash detection identifies and resolves potential conflicts between the formwork and other components, facilitating a smoother construction process.
Are you looking for 3ds Max-based solutions?
BIM ASSOCIATES helps you 3D-model your objects, furniture, buildings, and landscapes and enables you to create scenic renders and videos.
Step 3: Simulation and Analysis
The BIM model performs structural simulations, testing the formwork system’s ability to bear loads, handle concrete pressure, and maintain stability. Visualisation tools enable stakeholders to review and refine the formwork layout for greater efficiency.
These simulations minimise risks and ensure the design meets performance standards in real-world conditions.
Step 4: Material and Cost Estimation
Accurate quantity take-offs and cost estimates are generated directly from the BIM model, ensuring efficient resource allocation within budget constraints. Modular configurations are tested to optimise material usage, reduce waste, and cut costs. This phase aligns financial planning with project design and construction requirements.
Step 5: Collaboration and Coordination
A Common Data Environment (CDE) facilitates seamless collaboration and is a central platform for sharing the BIM model and related data. Architects, engineers, contractors, and suppliers can access up-to-date information, ensuring real-time communication, transparency, and swift incorporation of feedback. This approach enhances decision-making and reduces errors.
Step 6: Prefabrication and Pre-Assembly Planning
Detailed shop drawings and manufacturing instructions for modular formwork components are generated from the BIM model. These instructions guide off-site production to precise specifications.
Logistics planning for prefabrication, including scheduling, transportation, and quality checks, streamlines the process. Pre-assembling parts off-site minimises on-site work and accelerates installation.
Step 7: On-Site Implementation
Assembly guides derived from the BIM model facilitate efficient installation of the modular formwork on-site. Real-time monitoring with BIM tools allows for immediate adjustments, ensuring construction adheres to the design. This stage capitalises on the meticulous planning and precision established earlier.
Step 8: Post-Implementation Review
The final structure undergoes rigorous quality checks to confirm alignment with the design. The BIM model is updated to reflect the completed structure, creating a digital twin. This twin is valuable for facility management, maintenance, and future renovations or expansions.
By adhering to this systematic process, modular formwork projects achieve exceptional precision, efficiency, and collaboration, delivering high-quality results that meet the demands of modern construction.
If you want to further enhance these outcomes, specific software and tools are essential to streamlining the design and execution of concrete modular formwork.
Also read: A Guide to Building Information Modelling (BIM) Impact on Modern Construction Industry.
Software and Tools Used for Concrete Modular Formwork
Modular formwork with Building Information Modelling (BIM) depends on various software and tools that support different stages of design, analysis, and construction. These tools improve precision, collaboration, and efficiency to ensure the successful completion of projects.
Let us look at the key software and tools commonly used in the UK for this purpose.
1. Autodesk Revit
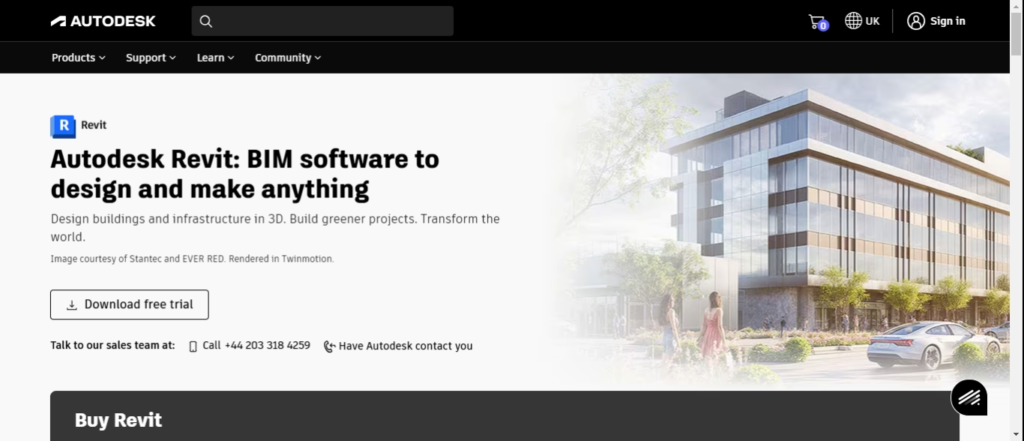
Autodesk Revit is a key tool for implementing BIM in modular formwork. Its parametric modelling features ensure that any changes to formwork dimensions or configurations are automatically reflected throughout the model, reducing errors and enhancing design consistency. Revit is beneficial for modular formwork because it can model prefabricated components and generate shop drawings.
2. Navisworks
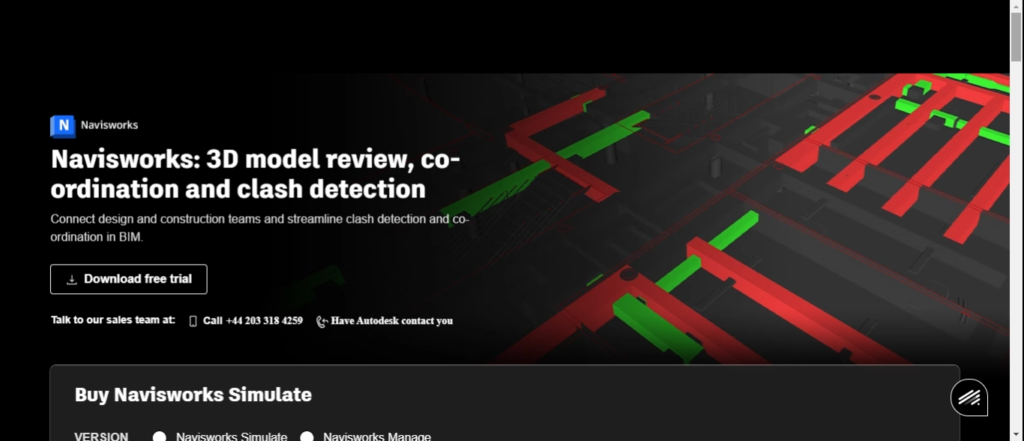
Navisworks is crucial for project review and clash detection in the modular formwork implementation process. It combines models from different disciplines to identify and resolve clashes between formwork systems and other structural or MEP components. Navisworks also offers 4D simulation, which integrates construction schedules with the BIM model, allowing teams to visualise the assembly sequence of modular formwork.
3. Tekla Structures
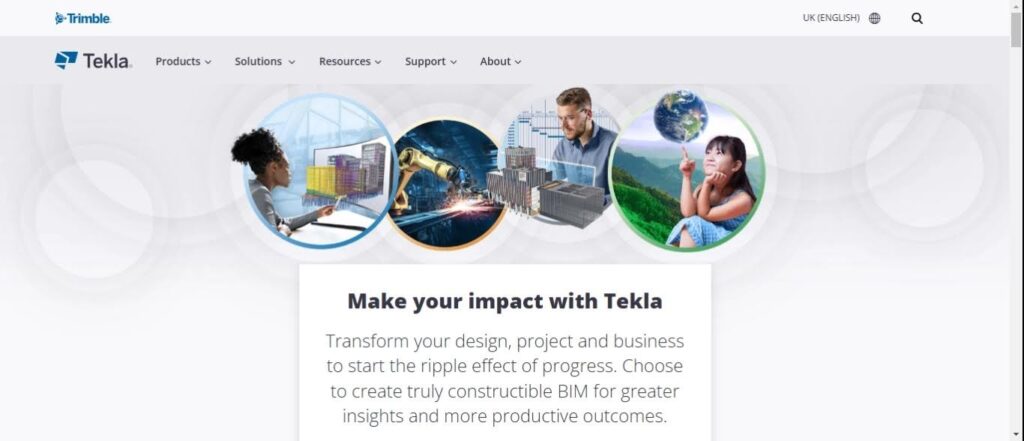
Tekla Structures, created by Trimble, is a popular tool for designing and detailing structures. This makes it perfect for modular formwork projects. Tekla helps design parts like concrete and steel components that are key to formwork systems. The software also creates accurate drawings and instructions for building the parts, which makes the prefabrication and pre-assembly processes faster and easier.
4. Dynamo for Revit
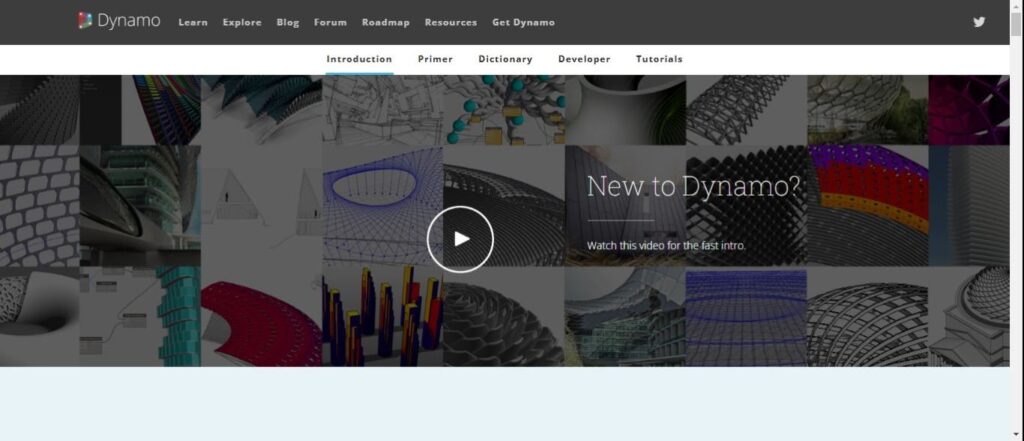
Dynamo is a visual programming tool that helps automate repetitive tasks and customise modular formwork designs. It allows users to create parametric scripts that automatically arrange formwork panels, spacers, and ties. This makes the design process faster and more accurate.
5. Solibri Model Checker
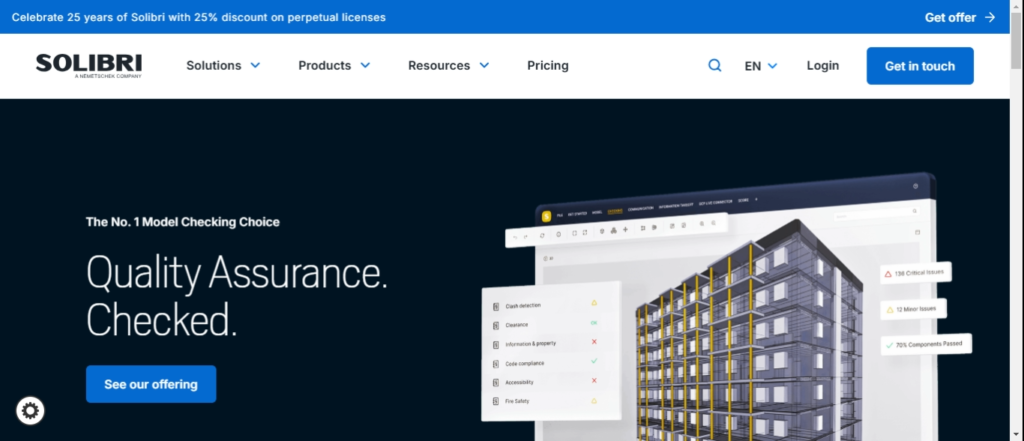
Solibri is a tool to check BIM models for accuracy and compliance in modular formwork projects. It ensures that designs meet specific standards, such as the UK’s Building Regulations 2010 and Eurocode 2 for concrete structures.
6. Trimble Connect
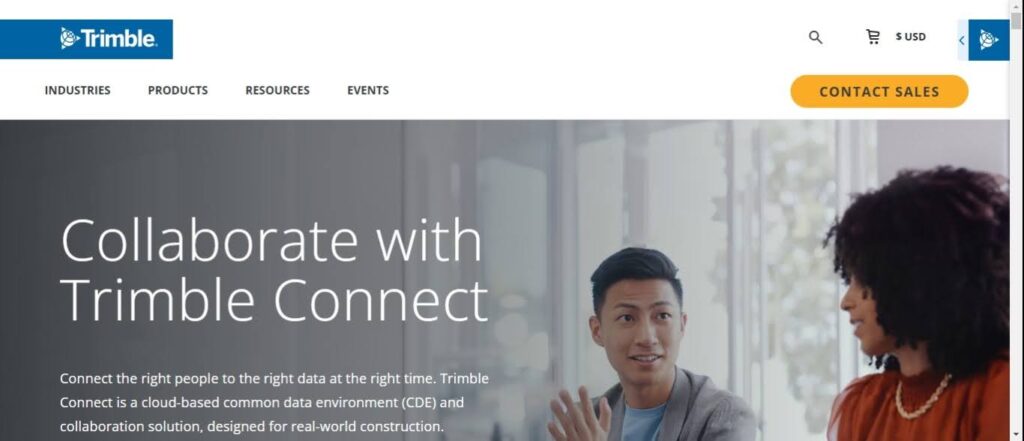
Trimble Connect is a platform to share and manage BIM models and project data during the modular formwork process. It acts as a Common Data Environment (CDE) that helps teams coordinate prefabrication and on-site assembly tasks more effectively.
7. Bentley Systems
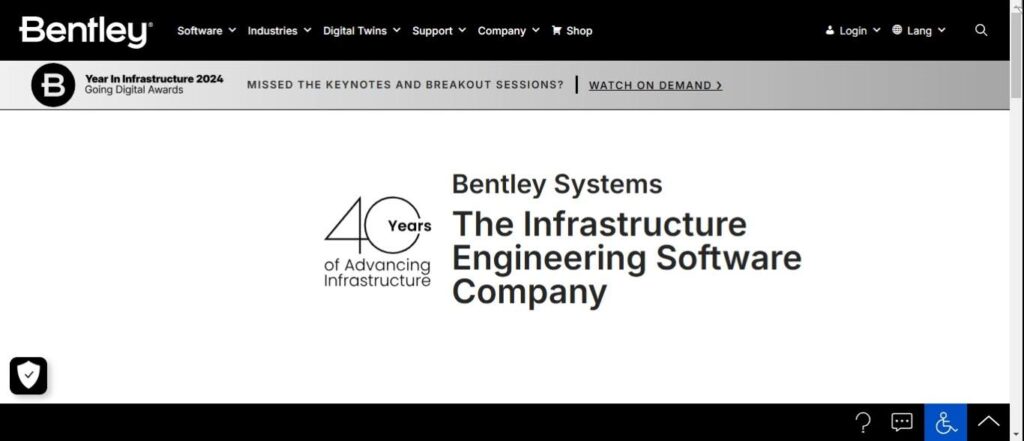
Bentley’s tools, like OpenBuildings Designer and OpenRoads, are used for complex building and infrastructure projects that involve modular formwork. Bentley’s iTwin platform helps create digital twins, which can be used in modular formwork projects to manage the entire lifecycle and ongoing maintenance.
The right software and tools are crucial for maximizing the efficiency of modular formwork systems. However, to ensure compliance and safety, it’s equally important to consider the regulatory standards that govern their use in the UK. These guidelines help maintain quality and consistency across projects.
Regulatory and Standards Considerations for Modular Formwork in the UK
In the UK, using BIM for modular formwork must follow several regulations and standards to ensure safety, quality, and sustainability. Here are the key factors to consider:
- Building Regulations 2010: These regulations set the minimum design, construction, and safety standards in buildings. Modular formwork systems must meet structural integrity, fire safety, and energy efficiency requirements as outlined in Approved Documents. For instance, Part A is for structural safety, and Part B is for fire safety.
- ISO 19650 Standards: This international standard governs how information is organised and managed using BIM. It focuses on collaborative workflows, using a Common Data Environment (CDE), and lifecycle management that aligns with the UK’s BIM Level 2 mandate.
- BS EN 1992 (Eurocode 2): This standard provides guidelines for designing concrete structures and ensuring modular formwork systems can handle load-bearing pressures and environmental conditions.
- BREEAM Standards: Modular formwork and BIM workflows should support the UK’s sustainability goals, including energy-efficient practices and low-carbon construction methods, to achieve high BREEAM ratings.
- Construction Products Regulation (CPR): Modular formwork components must meet CPR requirements to ensure CE marking for the materials used in construction projects.
- Health and Safety Regulations: The Health & Safety at Work Act and Construction (Design and Management) Regulations (CDM 2015) require formwork systems to be safe for workers. This safety should be ensured during assembly, operation, and dismantling.
Understanding the regulatory and standards considerations is key to ensuring the safety and legality of modular formwork systems. Equally important are the compliance measures that must be followed throughout construction to meet industry requirements and deliver successful projects.
Compliance Measures and Steps for Construction Projects
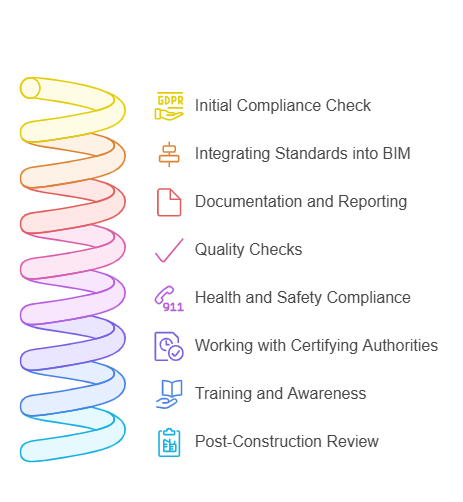
If you want to meet regulations and standards for construction projects using modular formwork and BIM, you should follow these steps:
Aspects | Effective Steps |
Initial Compliance Check | Review the project requirements to determine which regulations and standards apply, like local permissions and environmental assessments. |
Integrating Standards into BIM | Add relevant standards to the BIM models, such as calculations based on Eurocode 2 or sustainability goals like BREEAM. Use tools like Solibri to check the model’s compliance. |
Documentation and Reporting | In BIM platforms, keep detailed records, such as design plans, safety guidelines, and sustainability reports. Ensure these meet ISO 19650 standards for managing data. |
Quality Checks | Regularly inspect modular formwork components to ensure they meet the necessary standards, including CPR requirements. |
Health and Safety Compliance | Include safety measures in BIM simulations to identify risks before and during construction. Follow CDM 2015 guidelines during project planning. |
Working with Certifying Authorities | Work with certifying bodies early to get approvals and certifications, like CE marking for modular parts. |
Training and Awareness | Train everyone involved in the project on regulatory requirements so the design, construction, and inspection teams understand the compliance steps. |
Post-Construction Review | Use the BIM model as a digital twin of the finished structure to show ongoing compliance, especially for maintenance and lifecycle management. |
Implementing compliance measures effectively ensures that construction projects meet the required standards and proceed smoothly. Looking ahead, the future of concrete modular formwork and BIM in the UK presents exciting possibilities for further innovation and efficiency in the industry.
Future Trends in Concrete Modular Formwork and BIM in the UK
The future of concrete modular formwork is set to change dramatically with the use of Building Information Modelling (BIM) and new construction technologies. This combination improves efficiency, accuracy, and sustainability in the construction industry.
Here are the key trends shaping the future of concrete modular formwork and BIM:
- Emerging Technologies: New technologies like 3D printing for custom formwork, AI-driven design optimisation, and robotic assembly are reshaping modular formwork. These advancements improve precision, reduce waste, and make on-site processes more efficient.
- Sustainability Trends: Eco-friendly materials, like recycled plastics and low-carbon concrete, are becoming key in modular formwork. BIM tools are used more to model energy-efficient designs and assess their long-term environmental impact, helping meet net-zero carbon goals.
- Advancements in BIM Systems: Future BIM systems will include AI for predictive analytics, real-time integration of IoT data, and improved digital twin capabilities. These upgrades will increase accuracy, automate tasks, and enhance decision-making throughout construction.
Together, these trends are set to transform modular formwork and BIM, eventually boosting efficiency, sustainability, and innovation in construction.
Conclusion
Integrating concrete modular formwork with BIM revolutionises UK construction by enhancing efficiency, precision, and sustainability. This alliance accelerates processes, fosters collaboration, and ensures compliance with stringent regulations.
Tools like Autodesk Revit and Tekla Structures enable accurate modeling, compliance checks, and seamless transitions from design to construction. By embedding standards into every stage, BIM ensures modular formwork meets the UK’s high benchmarks, solidifying its leadership in sustainable, tech-driven construction.
Are you looking for BIM solutions?
BIM ASSOCIATES is your one-stop BIM Solution provider for Architecture and Structure. Their solutions help clients with better decision-making, cost-saving, efficient construction planning, and green earth initiatives. GO GREEN.
You might also like: BIM Levels and Stages of Development Explained
FAQs (Frequently Asked Questions)
1. What is modular formwork?
Modular formwork systems are built using standardised panels and components, which minimises the need to cut on-site materials. This speeds up the process and reduces labour requirements.
2. What are the different types of concrete formwork?
The different types of concrete framework include steel framework, plywood framework, fabric formwork, plastic formwork, and timber Formwork.
3. What is engineered formwork?
An engineered formwork system is made from prefabricated modules with a metal frame, typically steel or aluminum. The side facing the concrete is covered with a material that provides the desired surface texture, such as steel, aluminum, or timber.